News
May 2024
New design Zwergle-Duo Special for Storopack, the world's leading system supplier and service provider for flexible and tailor-made protective packaging (72 locations in 18 countries):
- 2 rotating turntables with universal holders for 2 chamber doctor blades up to 1250mm long
- 2 Tank system: Clean with alkaline cleaner
- Rinse with high pressure pump
- each tank with thermostatically controlled heating
Special challenge:
Since the customer requested that no solvent-based cleaner be used, greater mechanical effort was required:
- an additional (water) tank for rinsing after cleaning
- Additional tank heating to increase the cleaning effect of the alkaline cleaner
- more complex controls
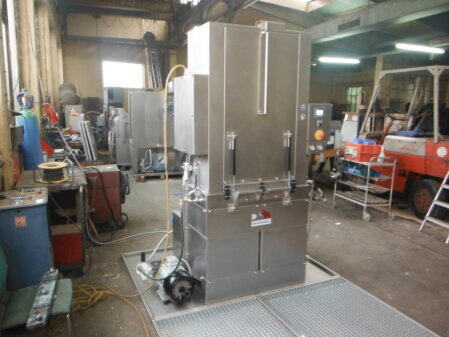
February 2024
Further development of SMT stencil cleaning systems:
After intensive testing, we have raised our SMT stencil cleaning systems to a new level in terms of cleaning time:
By using an extremely powerful washing pump with 160l/min in combination with our pat. Spray arms, the pat. Docking device for standard 25l plastic cleaning agent canisters and a fine filter, our systems are now able to create metal stencils in approx. 3 minutes. to be cleaned of solder residue and glue!!!
To our great surprise, this even works with “stretched” cleaner from KIWO (mixing ratio 60% cleaner, 40% water)
Thanks to our design, the cleaner heats up to 25 °C in approx. 30 minutes during washing mode (without heating!!)
At short notice, we demonstrate the performance of the system on site with your templates* and your operating resources.
(*Note: stencil size 555x555mm!)
After the system has been delivered, it can be inspected by our customer, who already has 12 of our systems in use, by making an appointment
New: October 2023
“Einfach-Genial” stripping system now has the option of entering sieve lengths for small sieves.
Advantage: Saving on stripping chemicals and shorter washing times
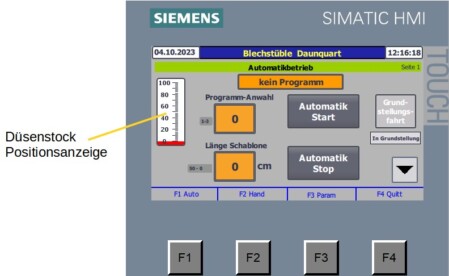
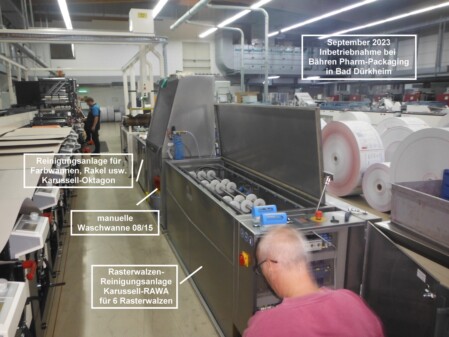
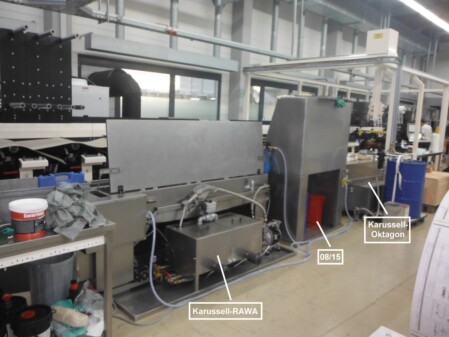
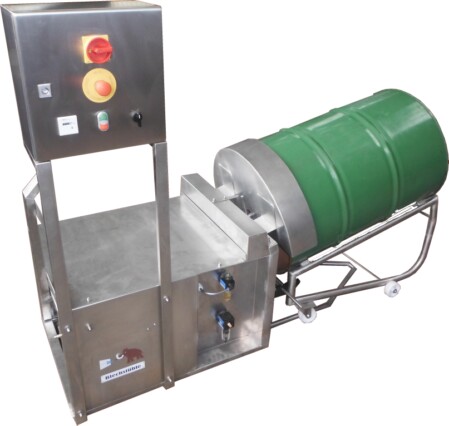
July 2023
Automatic barrel cleaning system "Fassbrause" for 200l barrels with mobile barrel tipping device made of stainless steel
for DE-VAU-GE
March 2023
Cleaning system set for
- Manual wash tub "08/15"
- auto. Parts cleaning system "carousel octagon"
for 6x ink trays, 6x squeegees and 6x fountain rollers
3. auto Cleaning system "Carousel-RAWA" for 6 anilox rollers:
- Washing system for 6 anilox rollers, horizontal assignment and drive for rotation of the rollers (compressed air drive)
- Occupancy 3 next to each other and 2 in a row
- Program selector switch for assignment with 2/4/6 rollers
- System with 3 functions: pre-cleaning with two-water cleaning agent in circuit with heated buffer tank (max. 40°C)
- High-pressure cleaning with hot water (max. 85°C) in circuit with insulated, heated buffer tank
- both buffer tanks with screw-in heater and thermostat control (from 10-85°C)
- Pre-cleaning with fixed nozzle assembly equipped with flat jet nozzles over the entire width of the anilox rollers
- Movable high-pressure and blow-out nozzle stick from right to left
- High-pressure pump with frequency converter for individual adjustment of the pressure
- cover with pneumatic lifting cylinders and foot switch actuation
- pneumatic 3-way valve at the outlet (wash tank/high-pressure water tank)
- high-pressure tank with automatic Filling device (float switch)
- 3 programs can be selected: for assignment with 2, 4 or 6 rollers
- Siemens PLC control
- required connections: electr. Connection 400V/32A, compressed air connection, fresh water connection, waste water connection
- Program Sequence:
- Open lid with foot switch
- Equip the system with rollers (position by position)
- Close the lid with the foot switch
- Press start button
- The drive for the rotation of the rollers starts
- The wash pump conveys the cleaner from the buffer tank to the spray arm and cleans the rollers for an adjustable period of time, the cleaner flows back into the buffer tank
- After the set cleaning time, the draining time begins
- After the adjustable draining time, the 3-way valve switches (washing tank/high-pressure water tank), the high-pressure pump conveys the hot water from the buffer tank to the mobile high-pressure nozzle assembly and cleans the rollers (first position 1, then 2, then 3 > depending on the program selection). The water flows back into the buffer tank*
- After the high-pressure cleaning, the roller is blown off with compressed air via the mobile nozzle assembly (first pos. 1, then 2, then 3)
- After blowing out, the 3-way valve switches again (high-pressure water tank/washing tank)
- program end
* After an adjustable cycle time, the high-pressure water tank is partially emptied via a solenoid valve and automatically refilled. This saves a lot of fresh water and requires far less energy to heat the water.
February 2023
Our latest project: parts cleaning system for
Task:
Cleaning of Porsche deep-drawn parts in a continuous process (system length max. 3m, belt speed approx. 1500mm/min), which come coated with adhesive oil directly from a 1600t-Schuler press.
After intensive tests with cleaners and solvents from countless manufacturers, we found that this approach would not lead to success.
The cleaner simply ran off the deep-drawn parts without any effect. Only after a longer exposure time, which unfortunately is not available to us in the continuous system, success was shown.
Based on our findings, we found a solution without the use of cleaners to largely remove the adhesive oil from the parts. We are also developing a simple oil separation device.
Of course, we submitted this solution to the patent attorney!!
November 2022:
The raccoon 2.0 SMD stencil cleaning system is now only supplied with rinsing.
Through intensive testing, we were able to increase the performance of our washing pumps from the original 70l/min to 160l/min.
In the future, all SMD stencil cleaning systems will have the self-priming washing pumps with a capacity of 160l/min!!!, of course in combination with our dockable 25l canisters (protected for use!!).
With this combination, the cleaner heats up by 8°C within 10 minutes during the washing process !!
In addition, the new generation raccoons have 20" stainless steel filters to ensure the higher flow rates and pressures.
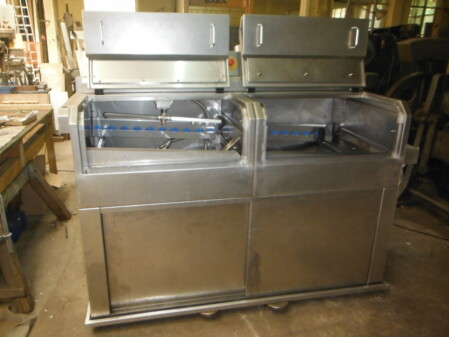
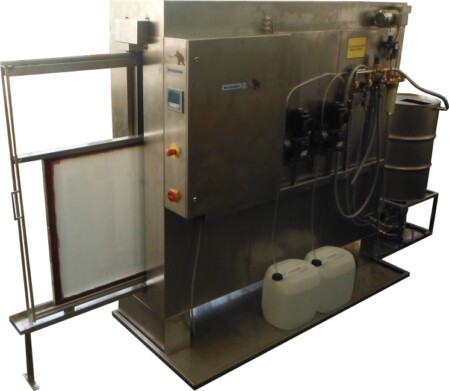
Screen de-coating system "Einfach-Genial" from now on always with 200l buffer tank to supply the high-pressure pump and sound-insulated cabin !!
2-chamber continuous stencil cleaning system "Waschbär 2.0" with new features:
- 2-part stainless steel lid for folding (lid of the drying chamber is thermally insulated!)
- Siemens LOGO display on the control panel for status display and for changing washing and drying times
- Movable spray arm for easier loading
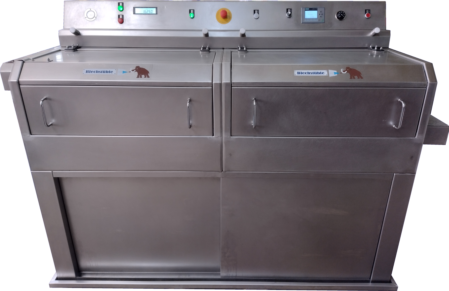
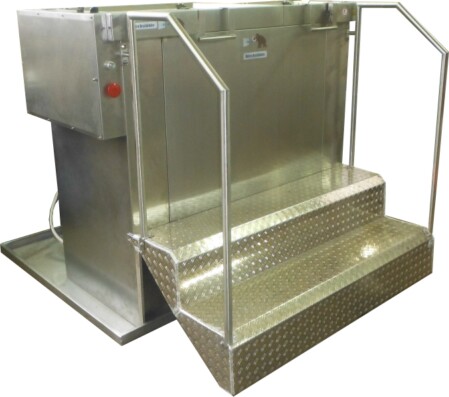
Parts cleaning system "Putzteufele" with two separate chambers.
1x whirlpool bath surrounded by compressed air for pre-cleaning.
1x washing chamber with 6 turntables for post-cleaning.
2x docking devices for standard 58l barrels (quick cleaning change without mess!)
Application protection number 20.2014 000 698.9
2x coarse filters to extend the service life
Fully automatic cleaning system for rotary screens with
2 dockable detergent containers. (Use protection number 20.2014 000 698.9)
Functional sequence: washing, blowing out the nozzle holder, draining, rinsing, blowing out the nozzle holder, draining
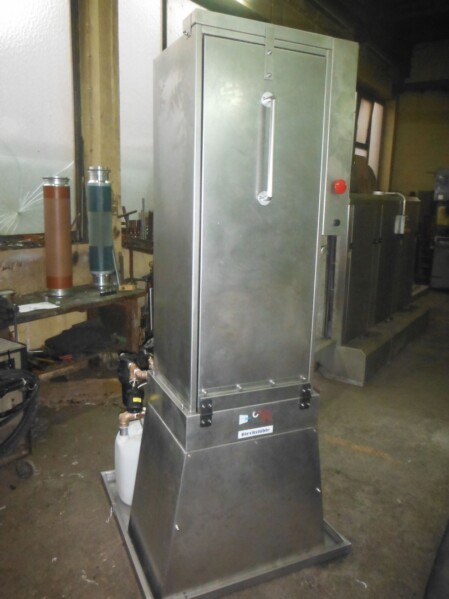
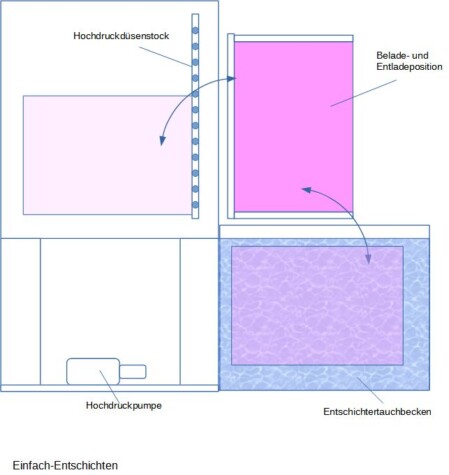
July 2021
New development of an automatic decoating system with decoating immersion basin: "Simply decoating"
Offers all the advantages of a dip tank: low consumption of decoating agent and the best results even with thick layers and coarse sieves!
- Patent pending already!
- manual loading and unloading, automatic program sequence
- 2 programs can be selected: decoating and developing
- low-speed high pressure pump
- High pressure spraybar assembly with Lechler high pressure nozzles
- Decoating program sequence:
The screen moves through the tilting mechanism into the decoating immersion tank
After the "immersion time" the screen moves into the washing chamber and is washed with high pressure (approx. 100 bar) and then back to the loading position and can be removed
- Develop program:
The screen moves into the washing chamber and is wetted with tap water
After the "wetting time", the screen moves back to the loading position and is washed off at approx. 10 bar
After the "wetting time", the screen moves back to the loading position and is washed off at approx. 10 bar
February 2021:
Problems with many (small) screen and textile printers are space problems and cost savings.
From the cumulative experience of 70 years ("Blechstüble" and cleaner manufacturer) the
"Einfach-Alles" cleaning system - not the first "All in One" cleaning system, but the first that actually works!
The system is of course already registered for use protection !, No. 20 2021 000 547.1
The system is a combination of the "Einfach-Sauber" screen washing system (with pat. Docking device)
and the stripping system "Einfach Genial"
The system is of course custom-made, changes to dimensions, program sequences, etc. are possible without any problems!
Brief description:
Screen washing and stripping / degreasing / developing system with one chamber
Washing screens with detergent in a circuit
The screen cleaner is docked under the system with a tried and tested docking device
The washing chamber is designed for optimal dripping / draining behavior of the cleaning media
Decoating and degreasing do not take place in a cycle
Stripping and degreasing concentrate is sprayed onto the screen with a chemical pump and, after an exposure time, fed into the sewer network with the high pressure water
The washing pump, chemical metering pumps and nozzle block drive are pneumatically driven
The high-pressure pump and the control cabinet are located outside of the Ex area
Various program sequences can be selected
Loading from the side !!
Loading opening is closed by a roller shutter
Manual post-treatment with a high pressure pump in the cabin possible without moving the sieve
Cleaner, stripper and degreaser chemistry are coordinated!
Cleaner: Emulsion cleaner flash point 56 degrees without cyclohexanone content
Decoater: Concentrate 1:20 1 canister results in approx. 100l decoater
Degreaser: concentrate 1: 5 to 1:10
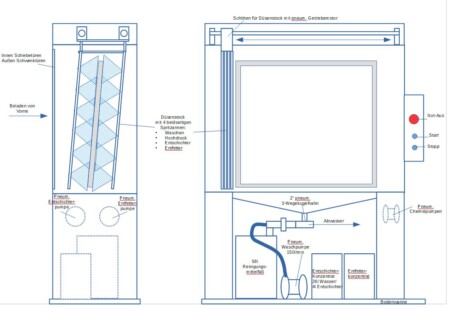
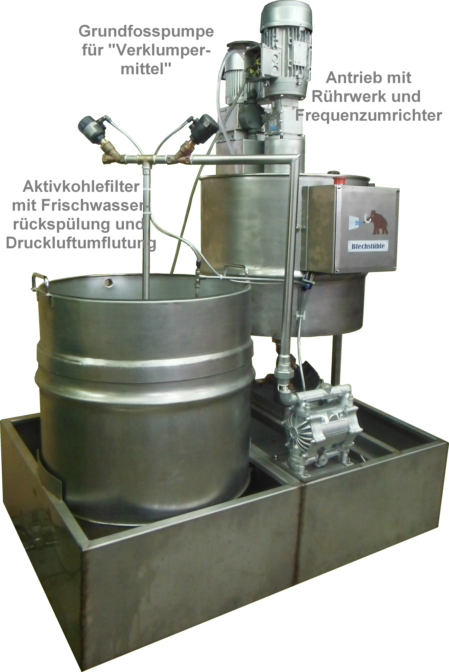
Test facility for the non-profit project Wasser 3.0:
"Jonathan" universal reactor
Use protection number 20 2020 004 171
Owner:
Blechstüble Daunquart, foreman, technician Alfred Daunquart
Wasser 3.0, junior professor, Dr. Katrin Schuhen, chemistry
researches new possibilities for wastewater treatment, in particular the removal of microplastics from wastewater.
For the ambitious project, we are jointly developing a mobile system for extensive test trials with a 100l reactor, fine and carbon filters.
Functionality:
- Reactor is filled with wastewater
- Gear motor with agitator creates a vortex
- Water 3.0 PE-X®plus is sprayed into the whirlpool
- After a short stirring time, the resting phase follows
- microplastic lumps are formed
- The drain valve is opened and the waste water runs through the cascade filter into the lower tub
- approx. 95% of all microplastic parts are removed from the water
- then the membrane pump conveys the wastewater into the activated carbon filter
- the activated carbon filter also removes drug residues and dyes
short movie at Youtube
A reactor with a capacity of 10,000 l is being planned based on the findings of the test facility for use in sewage treatment plants!
Parts cleaning system "Grauer Star" with integrated waste water solids filtration:
- for water-soluble paints
- 2 rotating spray arms driven by domestic water pressure
- for squeegees, flood squeegees, cups, etc ...
- Buffer tank with solids filtration (also available separately)
- Prevents the sewer pipe from becoming clogged with sludge
- Diaphragm pump with float switch function
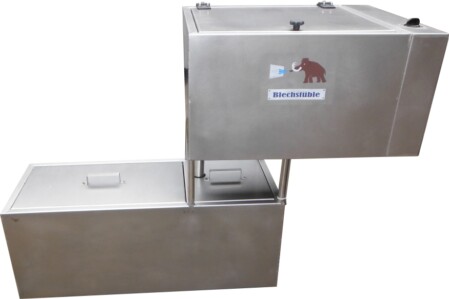
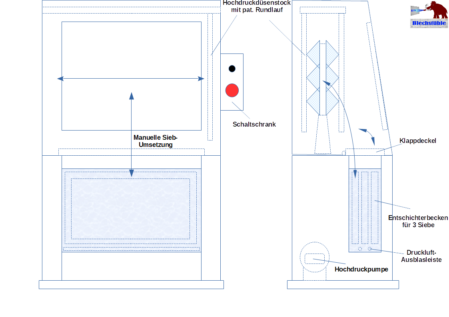
June 2020
Wash tub 08/15 with integrated decoating basin, especially for textile printers:
Stripping basin surrounded by compressed air for 3 sieves> long service life, low consumption
Stripping basin integrated under the washing chamber> little space required
Footprint approx. 1200x700mm
manual transfer from the stripping basin to the washing chamber
optionally automatic decoating or developing
High pressure pump 21 l / min at 150 bar
High pressure nozzle assembly with pat. Concentricity system
integrated LED rear wall lighting> optimal control
Inexpensive and efficient alternative to conventional chamber systems
Required connections: 380V power connection, house water connection, waste water connection
Challenge August-December 2019 for the company
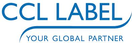
Development and production of a continuous cleaning system "Buffy" with 3 separate washing chambers for chamber doctor blades, ink trays and small parts
- Particular degree of difficulty: the washing baskets have to rotate around their own axis when being transported through the system
- registered utility model:
Continuous rotary cleaning system for
Chamber doctor blade printing units 20 2019 002 897.8
Docking device for 200l barrels 20.2014 000 698.9
The 10th washing system for the Holzkirchen plant !!!
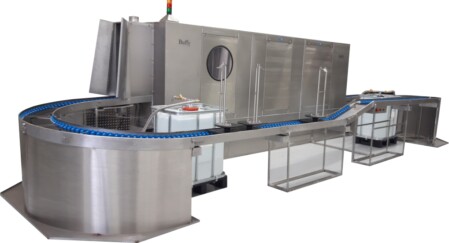
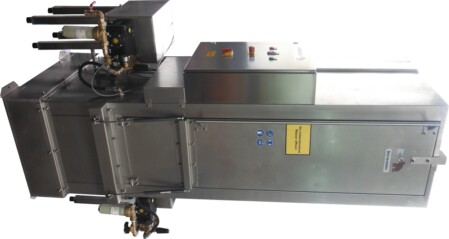
Challenge August-December 2019 for the company

Development and manufacture of a
"Zwergle" high-pressure cleaning system for printing stencils (max. Length 2500mm) and squeegees (max. Length 3500mm)
February 2018: Development of the 3-chamber conveyor washing system "Waschbär 2.5" for SMT stencils
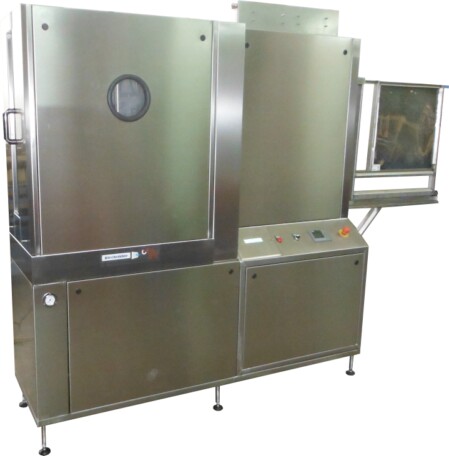
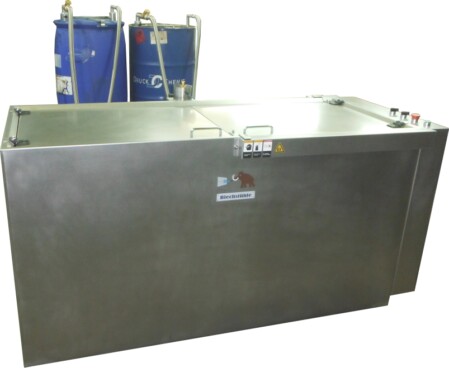
October / November 2017:
New development for CCL Label AG Switzerland:
Chamber doctor blade cleaning system "Karussell-Octagon 2.0" with two-water cleaner
with 2 separate 200l drums for washing and rinsing
October 2017
Washmammut 2.0
Consistent further development of the conveyor belt washing machine "Waschmammut" with a docking device for a 200l barrel
(Utility model 20.2014 000 698.9)
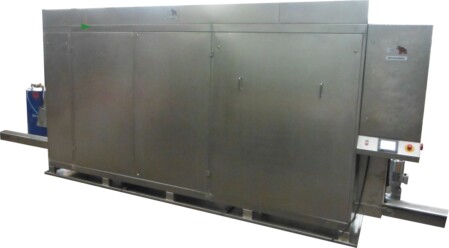
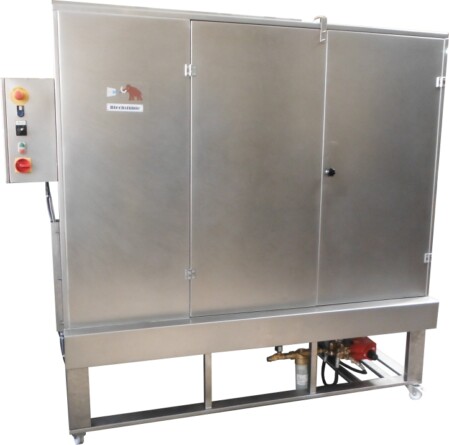
June 2017
High-pressure cleaning system "Drahtesel" with movable washing tower and rotating nozzle assembly! (registered for use protection!)
March 2017
Combination of automatic screen washing system "Einfach-Sauber" (with filter system)
and manual washing tub "08/15" (screen transfer with transport slide)
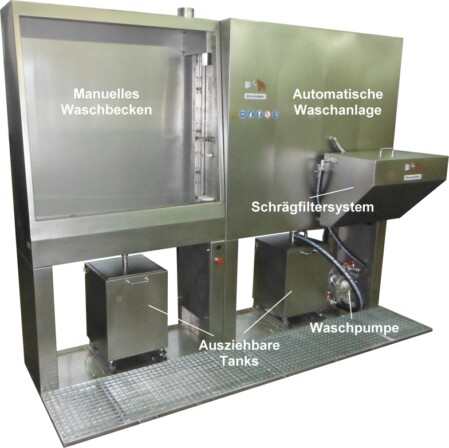
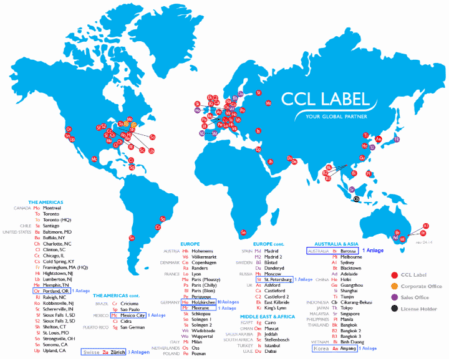
Our project for 2017:
UL-certification for rotary screen cleaning systems Karussell-Einfach and Zwergle and the cleaning system Oktagon for chambered doctor blades
(with patents for driven wheel and gear*) for CCL Label (global market leader for label solutions)
* 20 2011 005 529.9
20.2010.014 135.4
November 2016
"Zwergle / 2" rotary screen cleaning system with an additional station for cleaning flood squeegees
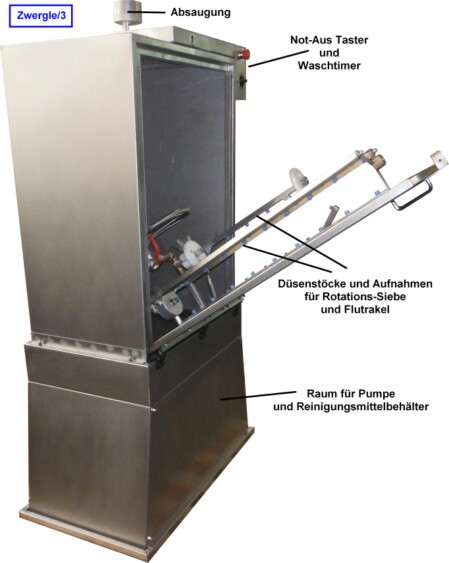
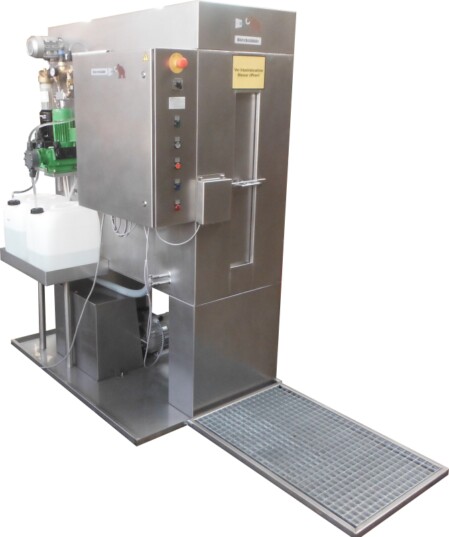
October 2016
Newly developed chamber system for decoating, degreasing and developing flat-bed screens
May 2015
New development for BASF:
"Riesenrad" cleaning system for tumbler screens up to 2650mm !! diameter
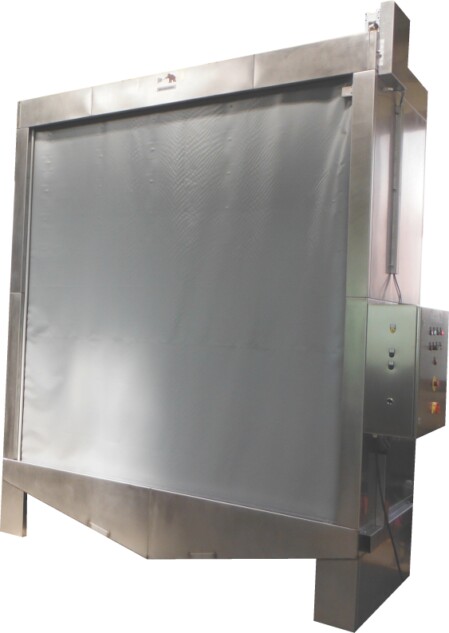
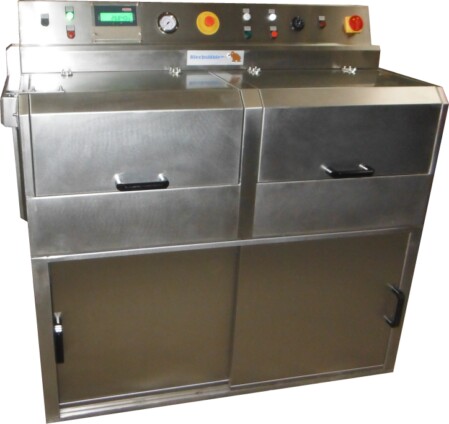
November 2014:
New generation of the fully automatic continuous SMD stencil cleaning system "Waschbär 2.0":
even easier - even better - even cheaper!
With registered use protection: No. 20 2014 010 114.0
August 2014:
Fully automatic rotating screen cleaning system "Zwergle", 2nd generation, for sieves up to 1500mm in length and 300mm in diameter
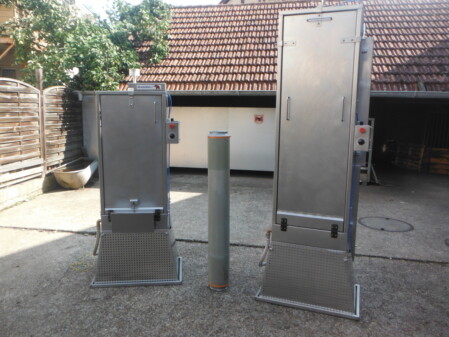
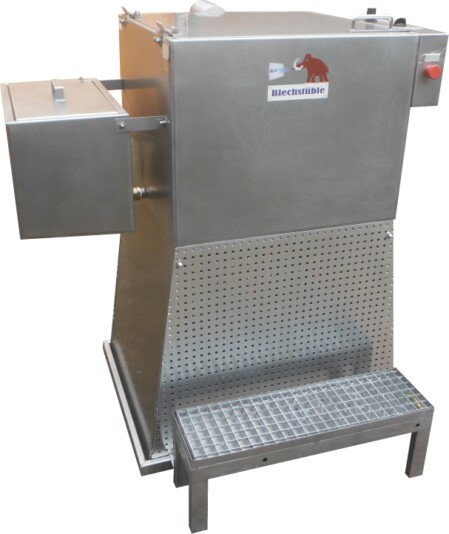
May 2014
Fully automatic cleaning system "Herbert" for parts cleaning during printing, pad printing and painting
- pat. Docking device
- pat. Inclined filter system
December 2013:
fully automatic parts cleaning system "Karussell-Oktagon":
- for all parts that arise during rotary printing, such as chambered doctor blades, ink trays, etc ...
- 8 stations with universal baskets for holding the parts
- Docking device for 200l and 58l barrels
- Use protection no. 20.2014 000 698.9
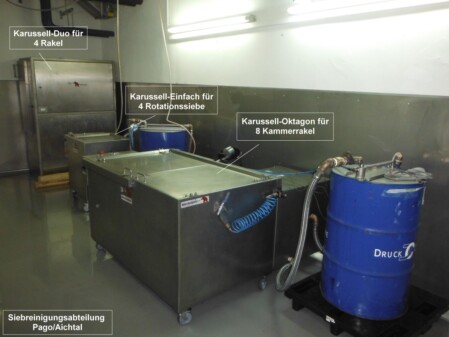
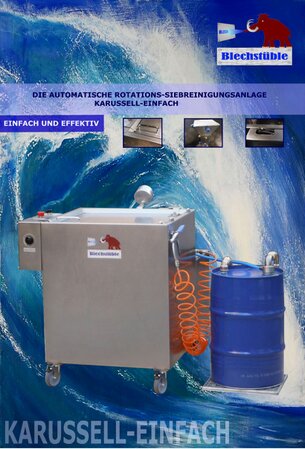
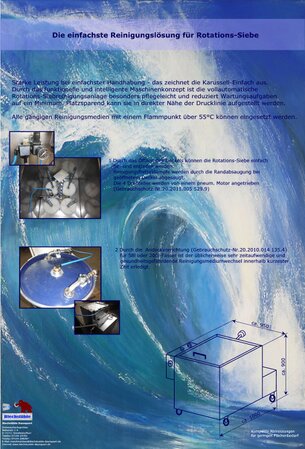
June 2013:
simple, fully automatic rotating screen cleaning system "Karussell-Einfach" without tank!
- 58l or 200l barrel (lid or bunghole barrel) with cleaner is simply docked (time required approx. 1 minute)
- pneum. control
- manufactured according to BGI 801 guideline
- Washing cabin for 2 or 4 rotating screens
- Edge suction via Venturi nozzle
- mobile on castors
- Complete nozzle assembly including supply line can be removed after loosening a nut
- Dimensions approx. 900x800x800mm> practical-square-best!
- Noise level below 70 decibels
- Required connections: compressed air connection
Exhaust air connection
Advantages for the customer:
- Inexpensive system, as the tank is completely omitted
- Lightning-fast, safe and clean change of the cleaning medium
- No more time-consuming tank cleaning that is hazardous to health!
- no unnecessary filling or emptying of the system
- When the cleaner is used up, the barrel with all dirt deposits is simply removed and replaced with a fresh barrel (the barrels can remain on the pallet!)