Produktionsstätte
Insights into our production:
The systems are completely handcrafted by our dedicated team in our Steinheim/Murr plant.
Only high-quality components are used, such as:
high pressure pumps
high pressure pumps
chemical pumps
Pneumatics
Pneumatics, compressed air diaphragm pumps, vane drives
electric pumps
PLC controls
safety relais, sensors
Flat Steel/High Pressure Nozzles
angle seat valves
gear motors
explosion-proof motors
Stainless steel sheets and tubes
CE declaration of conformity, risk assessment, operating instructions
June/July 2025 Vogtlandwerke "Einfach-Sauber"


March/April/May 2025:
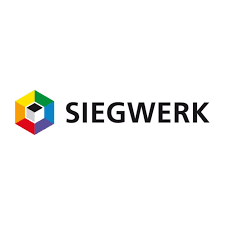
Major contract with Siegwerk Backnang:
Siegwerk is an international, market-leading manufacturer of printing inks and coatings for all types of packaging, as well as magazines and catalogs.
Siegwerk is headquartered in Siegburg (Germany) and is represented in more than 30 countries.
A total of three cleaning systems: one "Oktagon" for cleaning hobbocks, one "Herbert" for parts cleaning, and one "Fassbrause" for cleaning 100/200l drums.
Cleaning room fully equipped with stainless steel tanks and gratings (30x10).
KIWO 789E (flash point 80°C) is used as the cleaning agent.
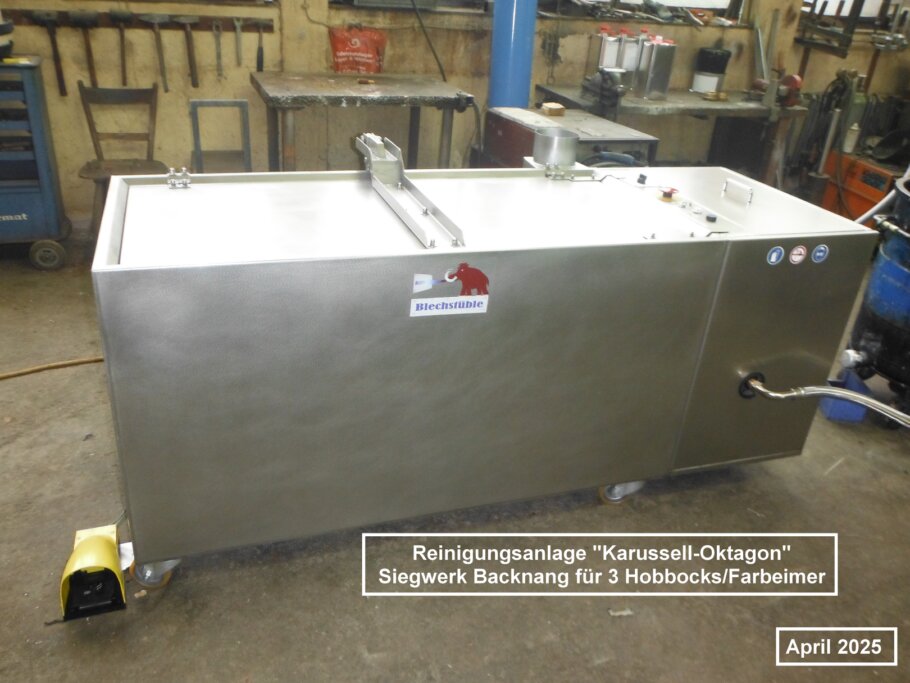
Task February 2025:
Development of a cleaning solution for DEKRA Stuttgart to remove inspection stickers and touch-up markers from stainless steel gauges.Extensive washing tests were conducted using various cleaners from well-known manufacturers (solvent, alkaline, and two-aqueous cleaners) and hot, high-pressure water.The best results were achieved with KIWO's liquid paint stripper 5544.
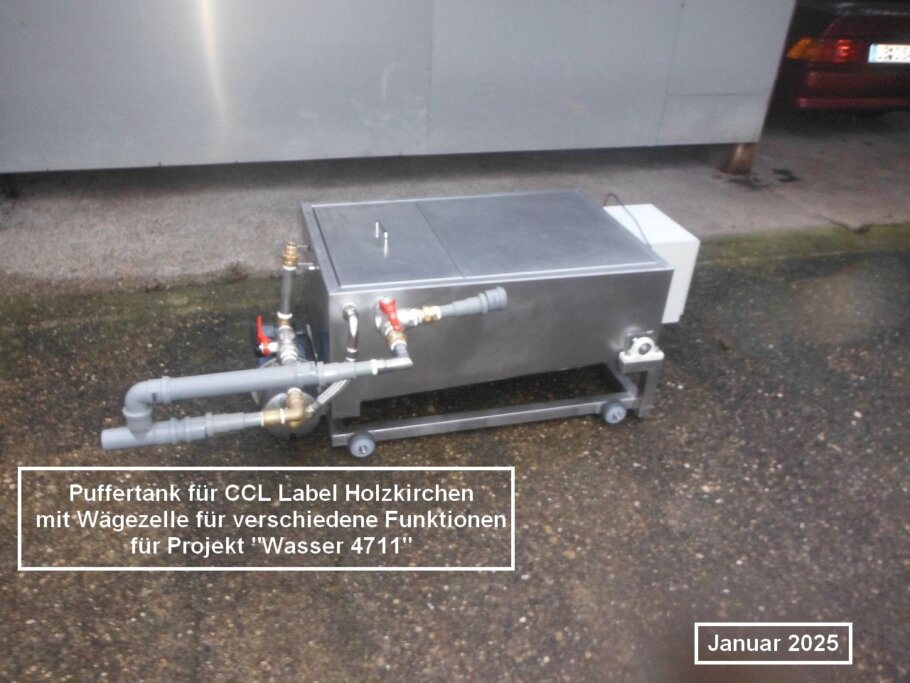
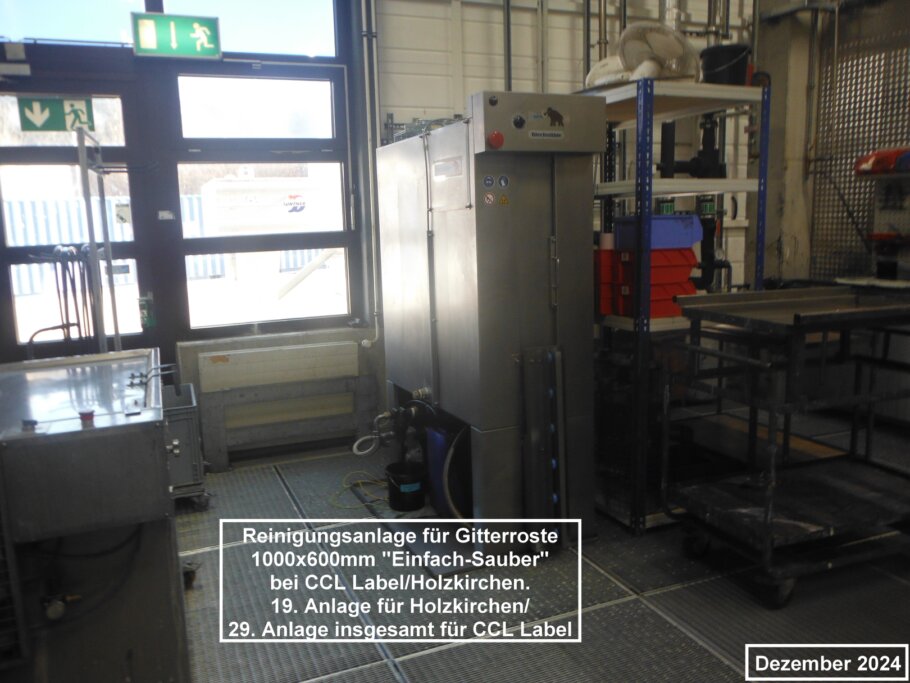
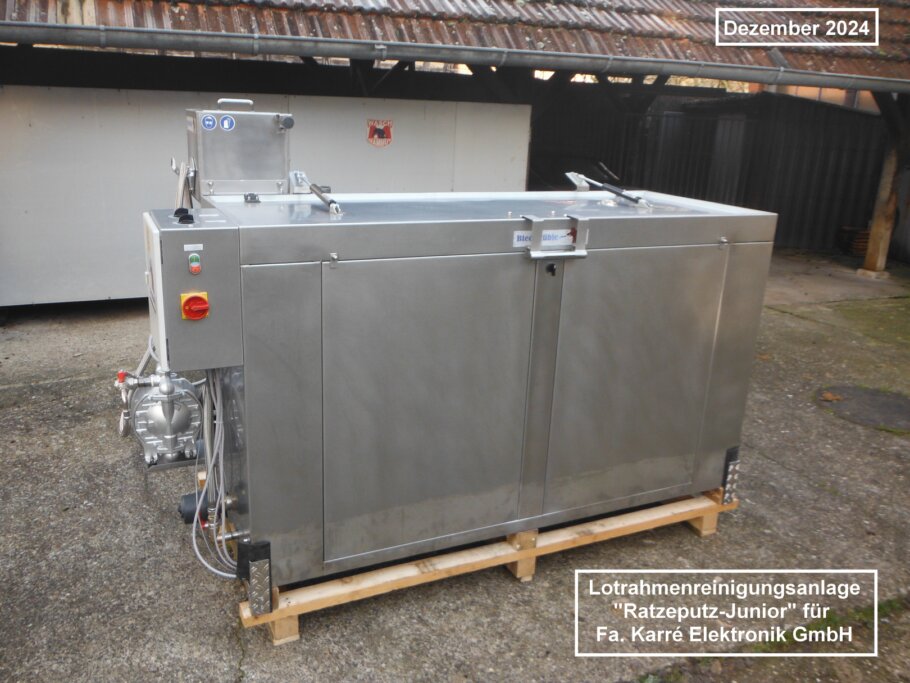
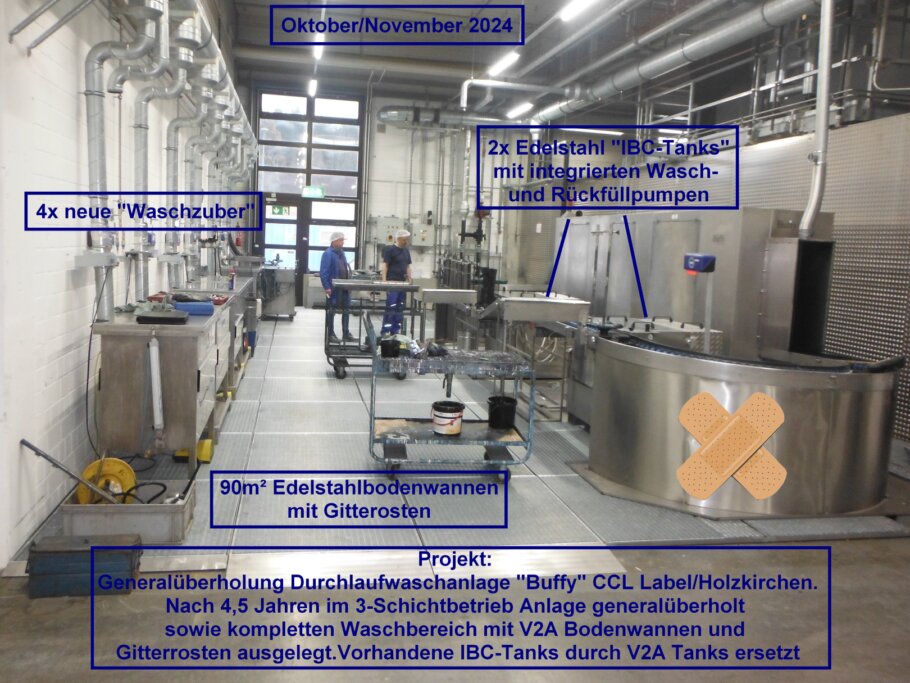
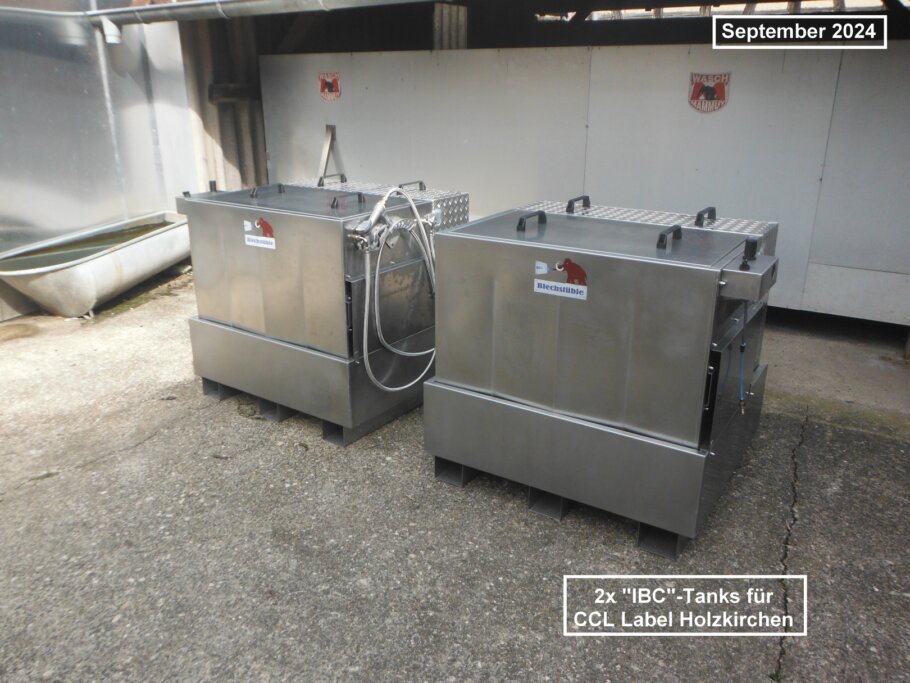
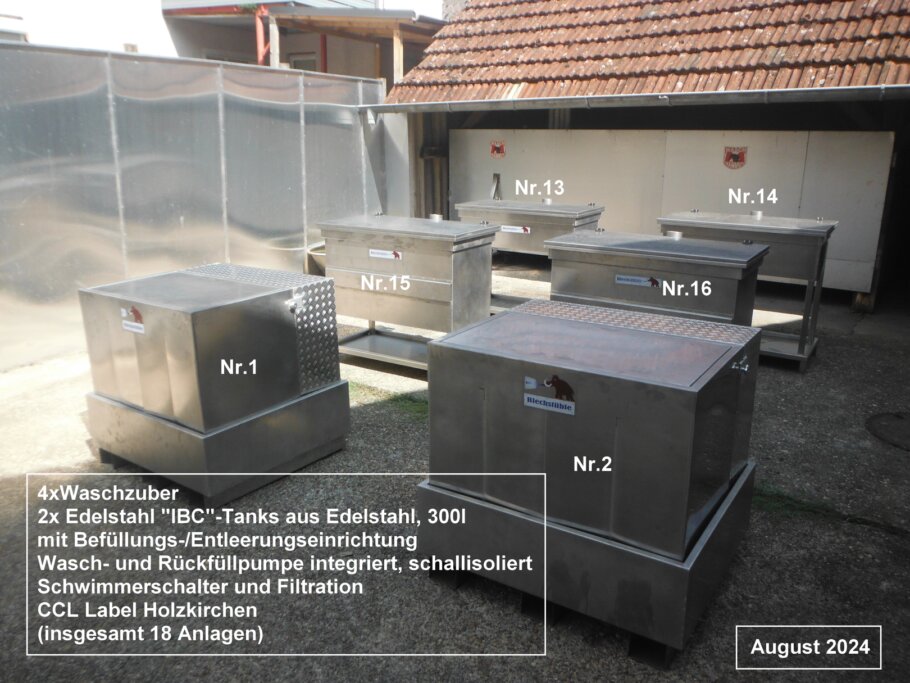
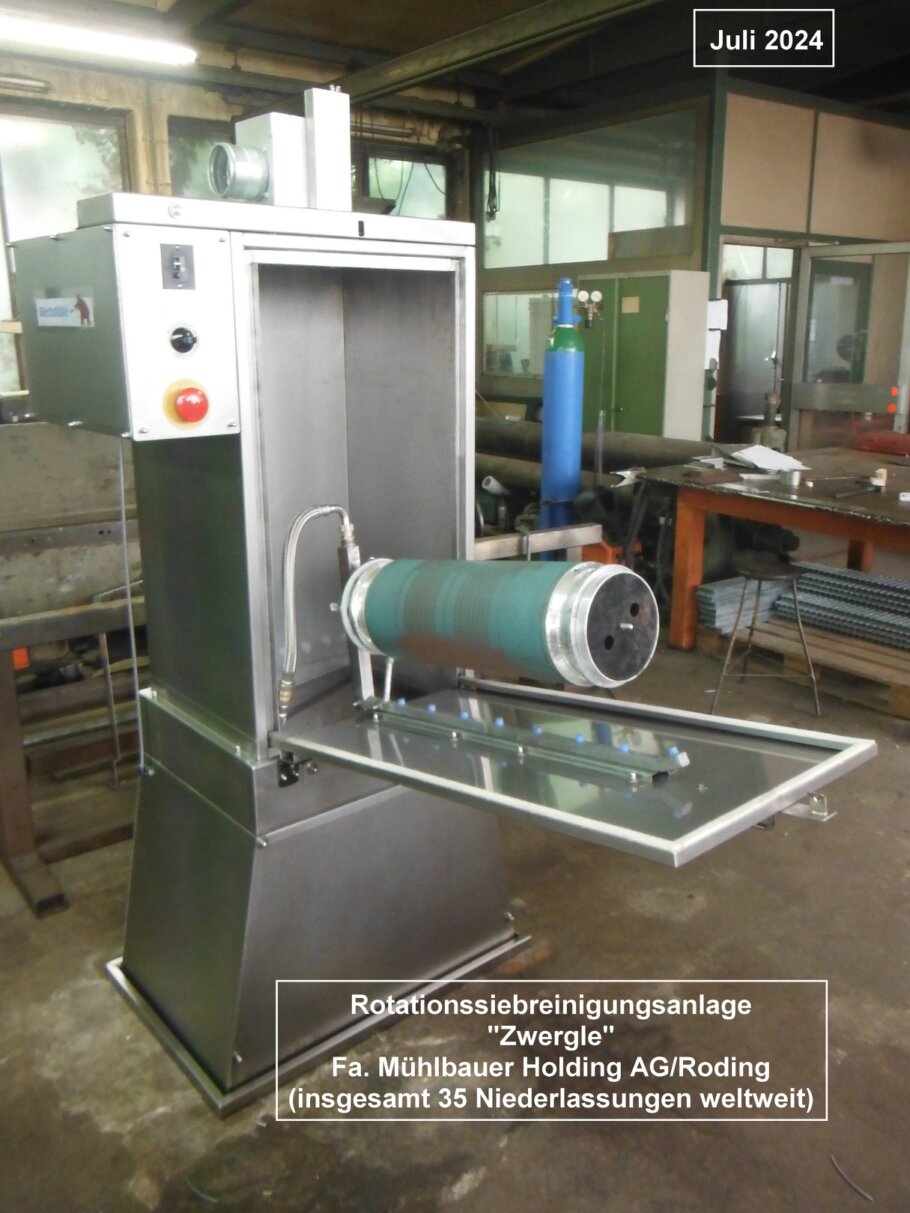
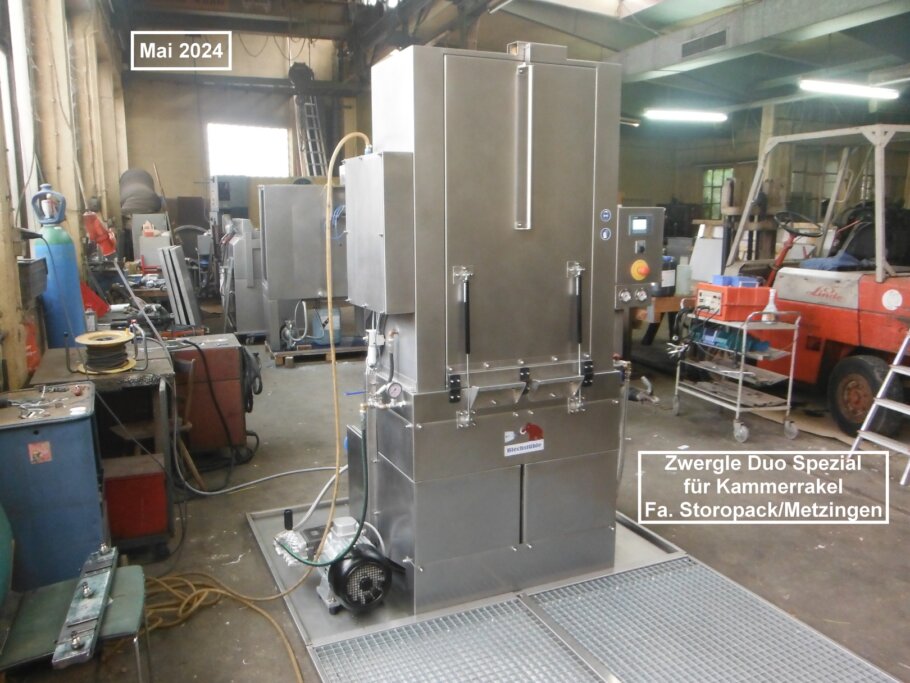
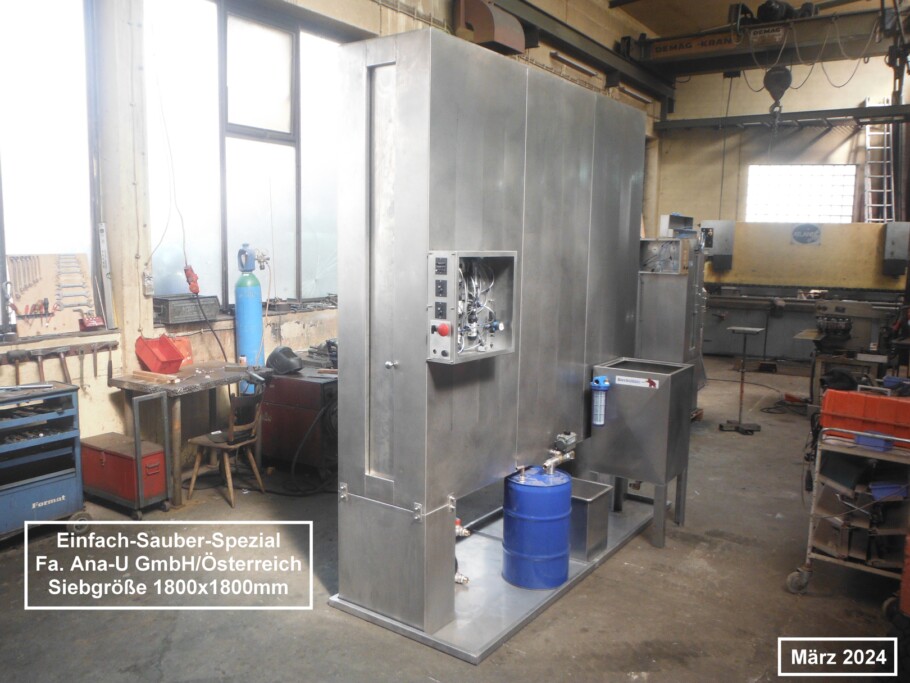
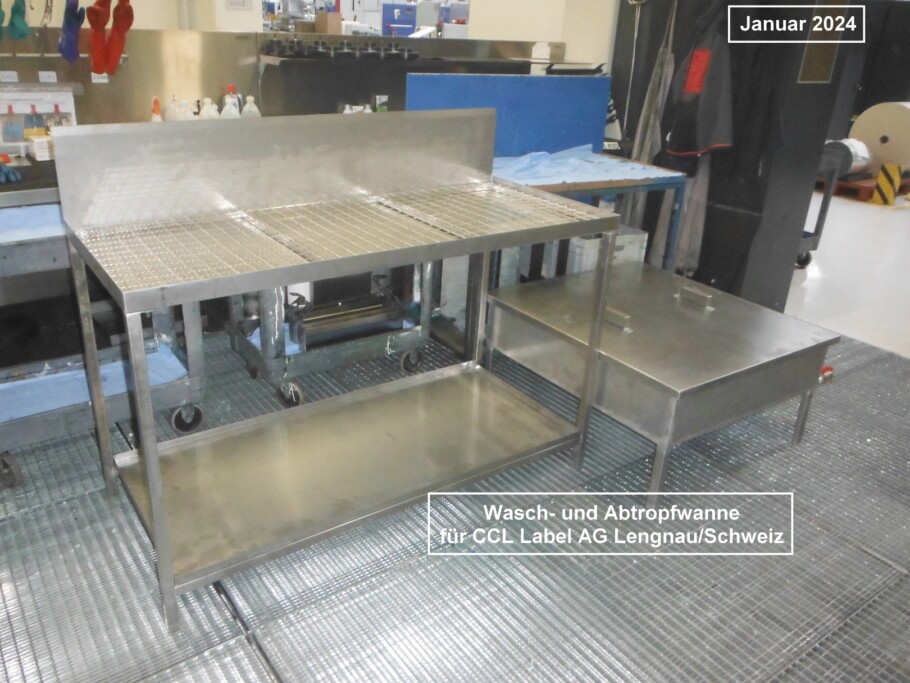
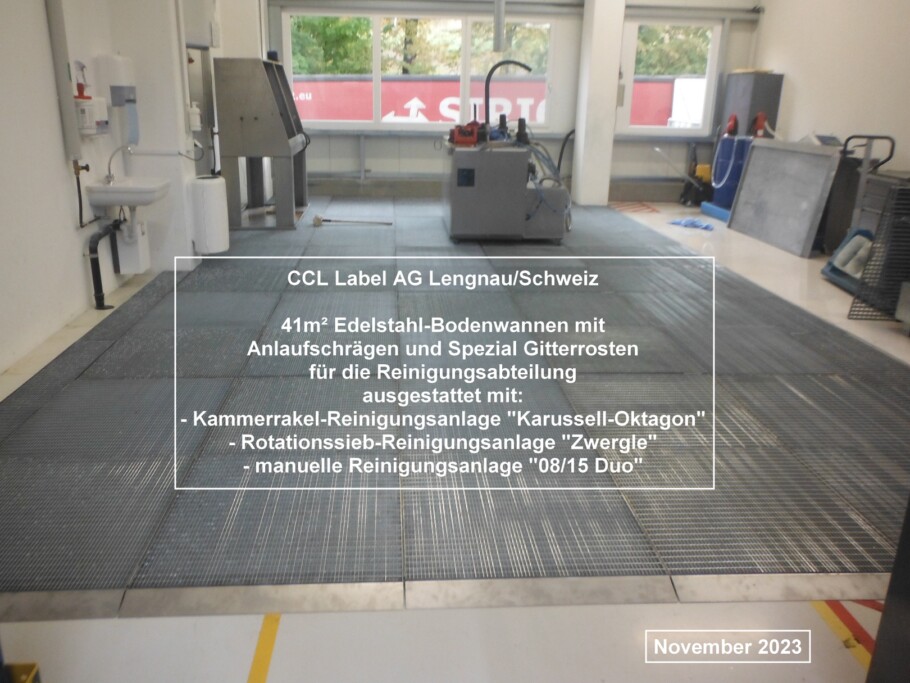
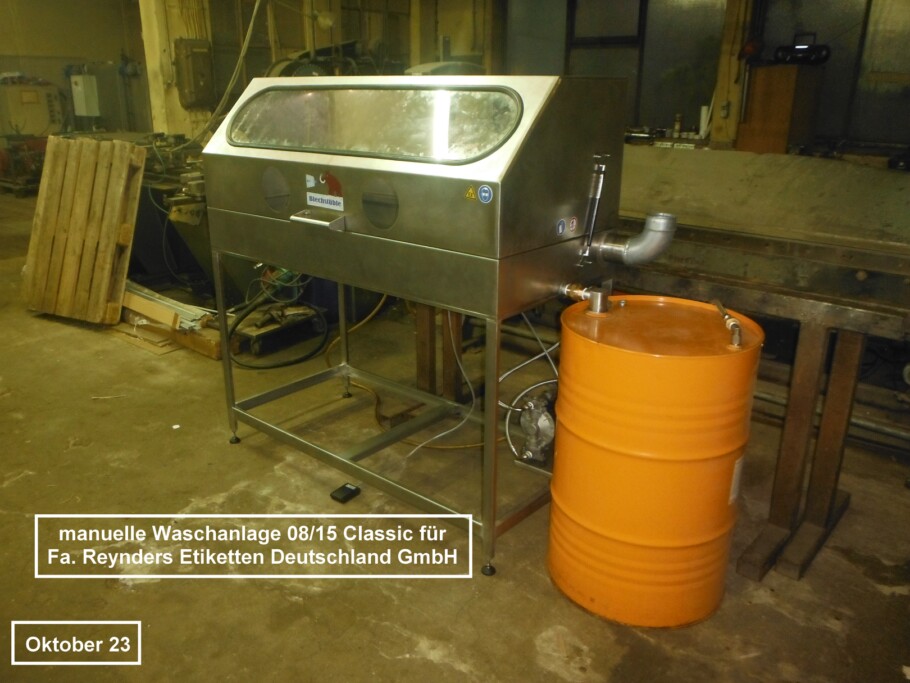
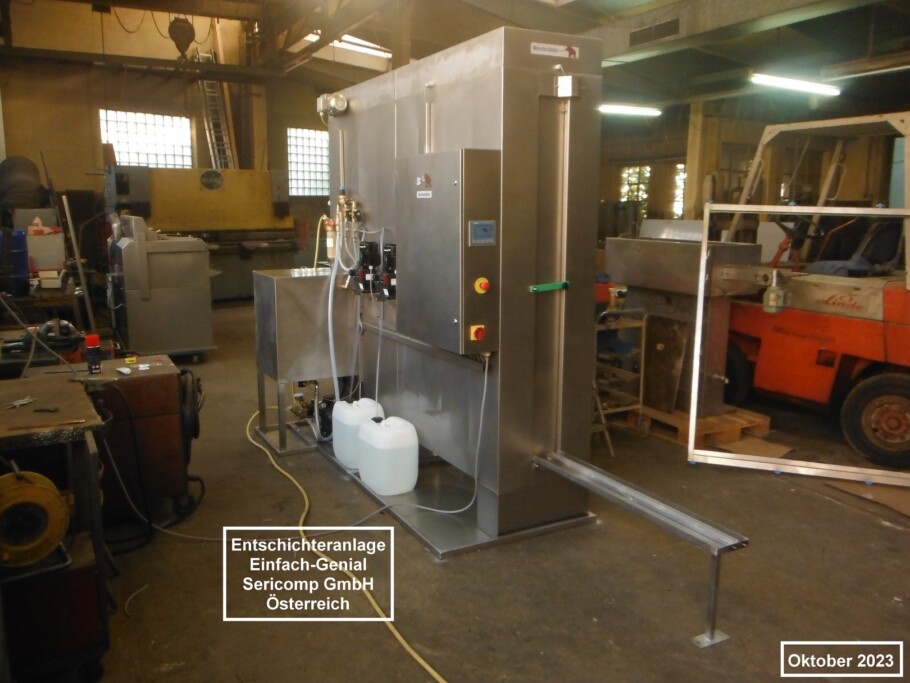
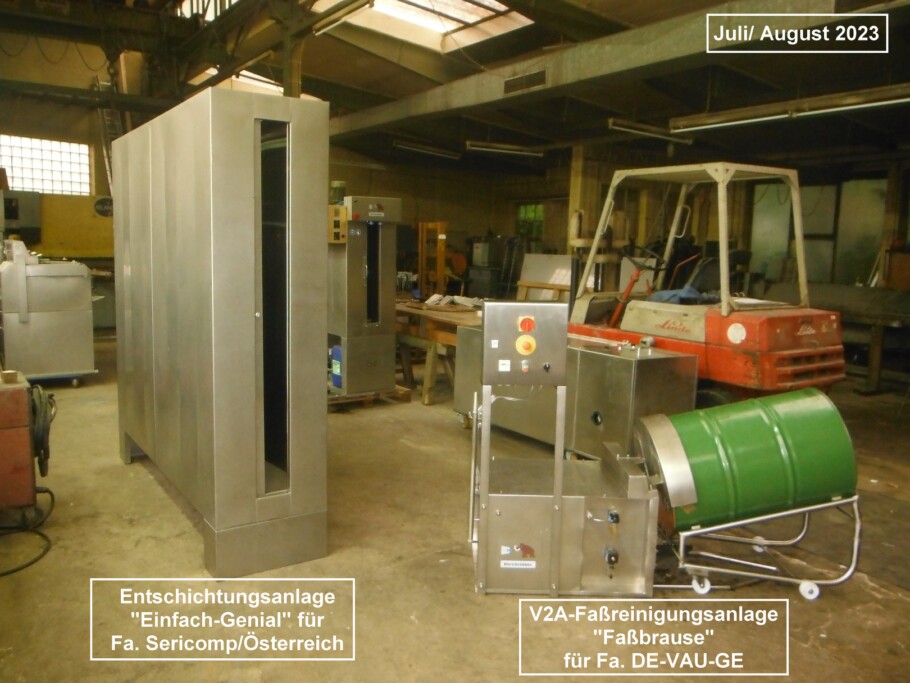
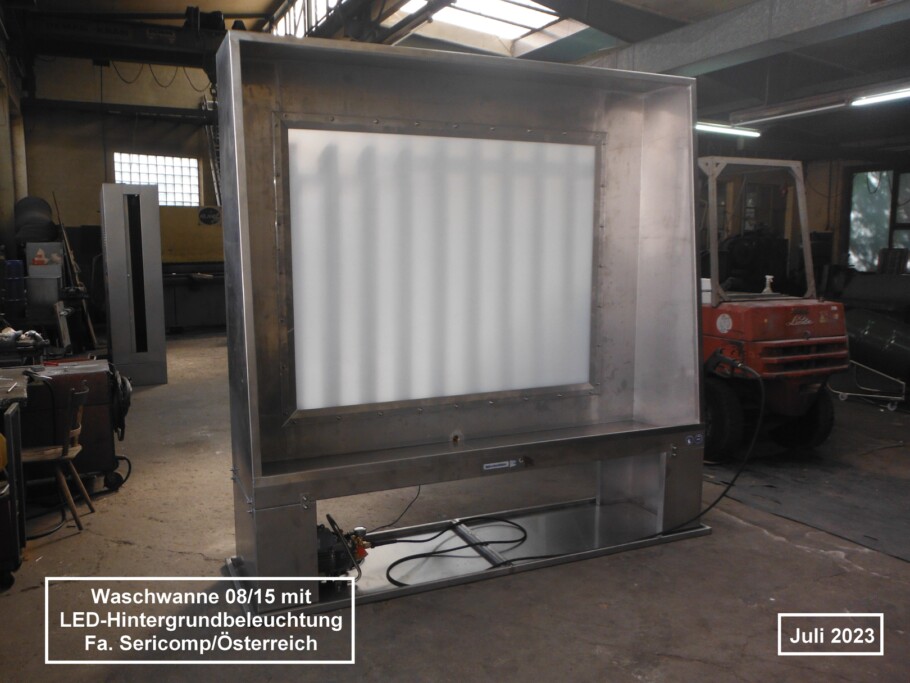
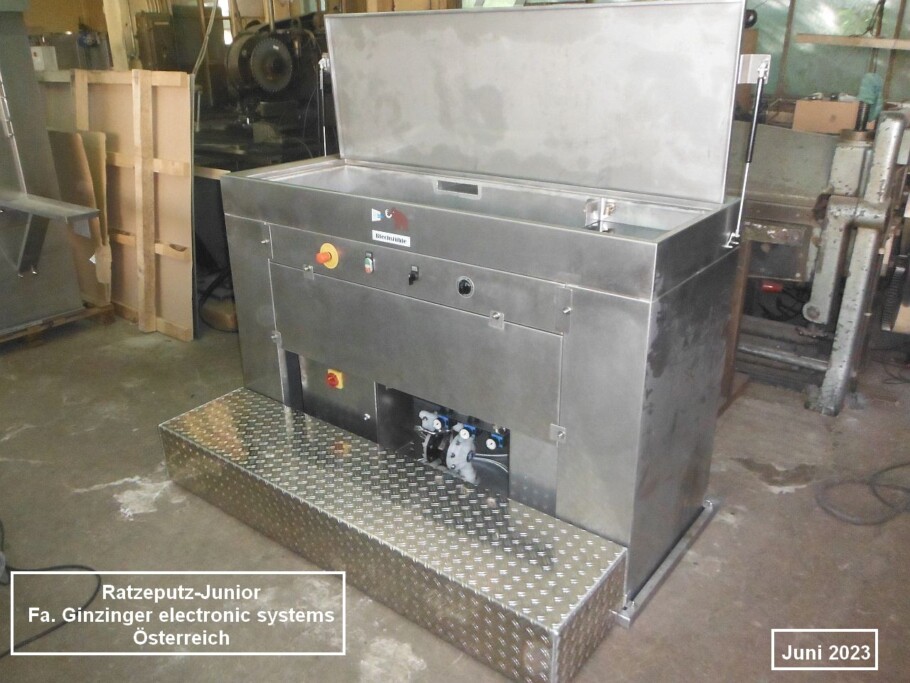
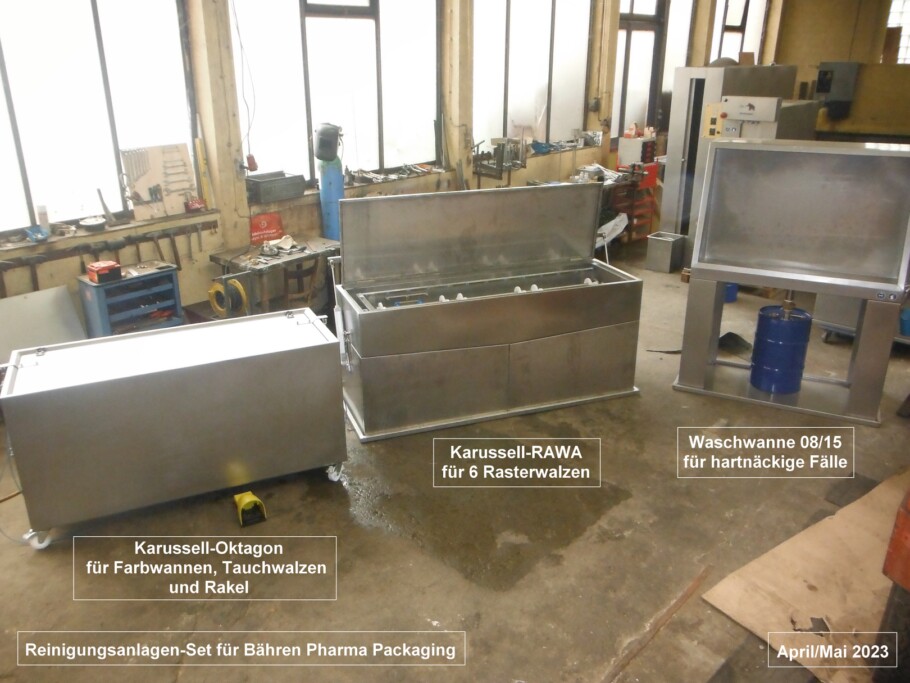
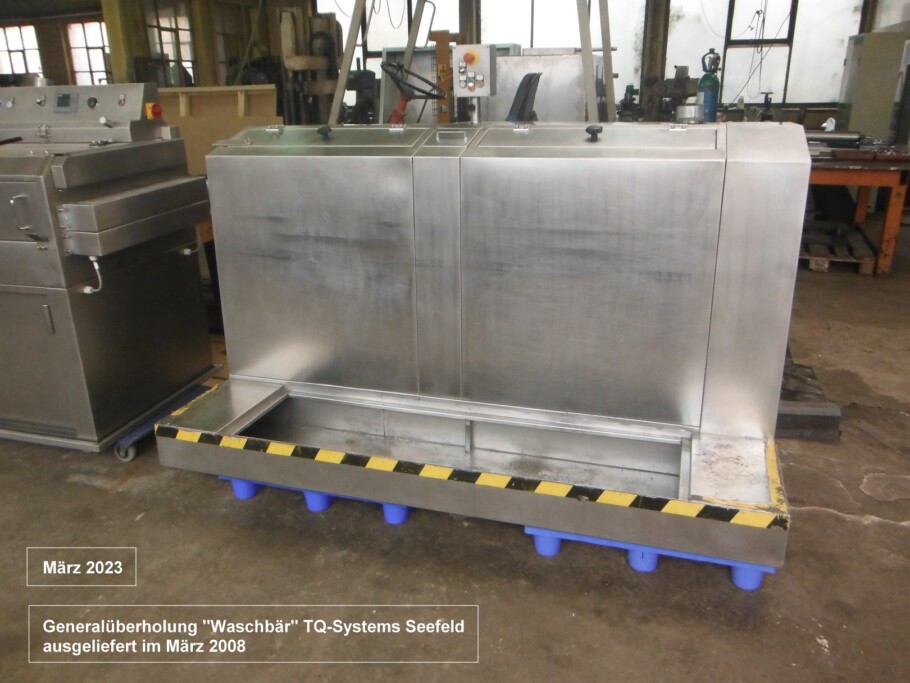
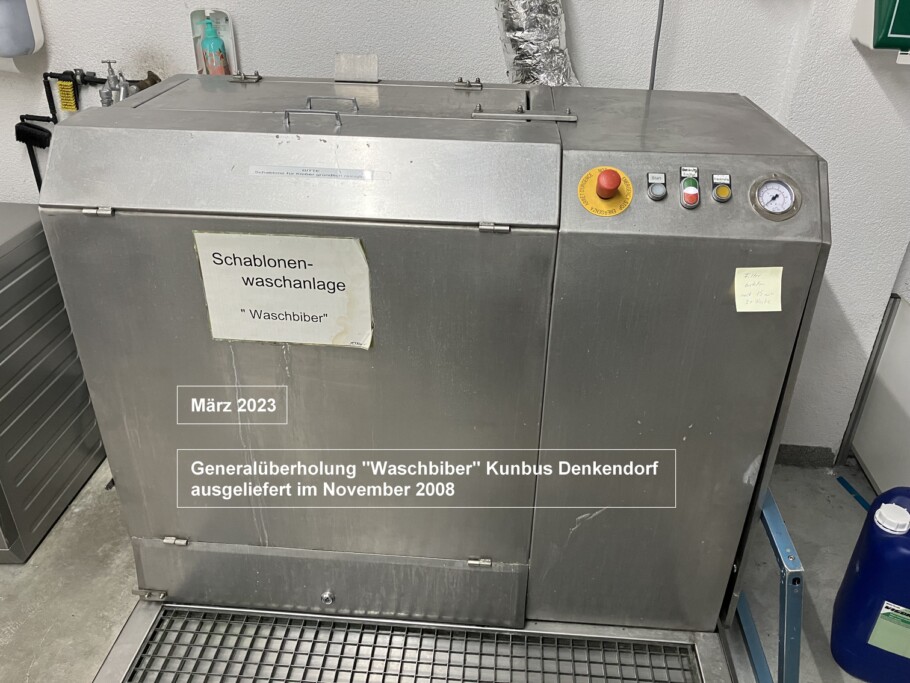
February 2023
Our latest project: parts cleaning system for ElringKlinger
Task:
Cleaning of Porsche deep-drawn parts in a continuous process (system length max. 3m, belt speed approx. 1500mm/min), which come coated with adhesive oil directly from a 1600t-Schuler press.
After intensive tests with cleaners and solvents from countless manufacturers, we found that this approach would not lead to success.
The cleaner simply ran off the deep-drawn parts without any effect. Only after a longer exposure time, which unfortunately is not available to us in the continuous system, success was shown.
Based on our findings, we found a solution without the use of cleaners to largely remove the adhesive oil from the parts. We are also developing a simple oil separation device.
Of course, we submitted this solution to the patent attorney!!
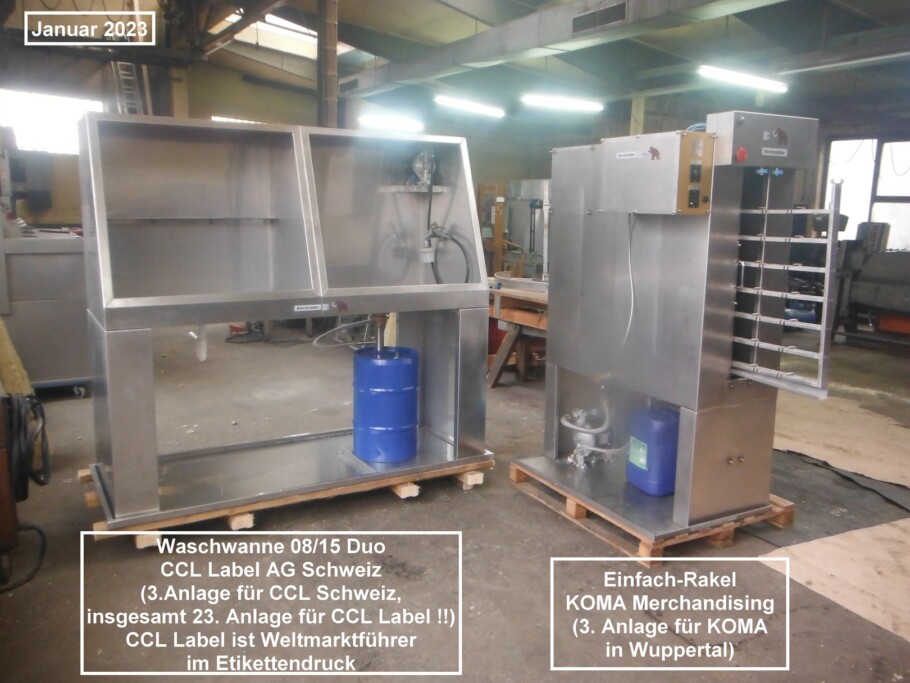
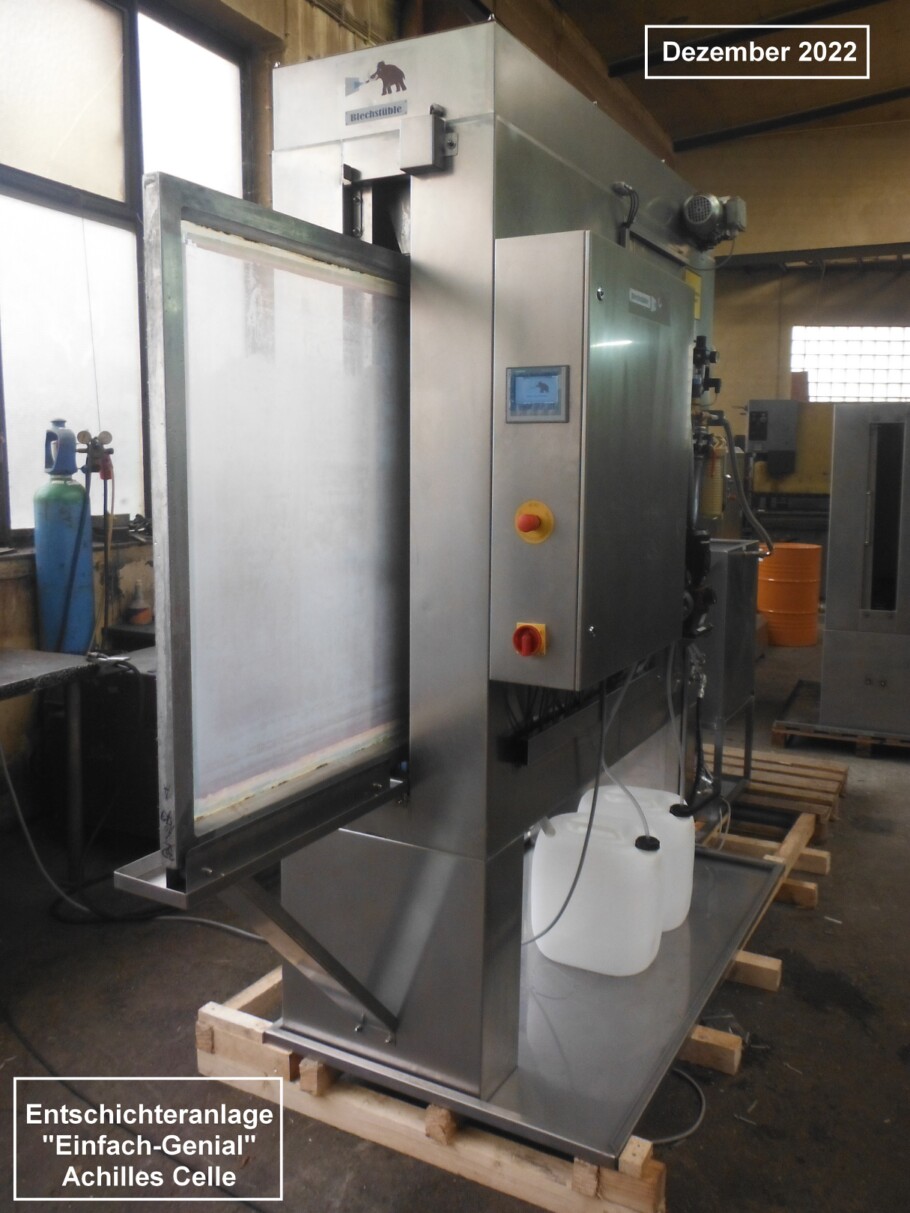
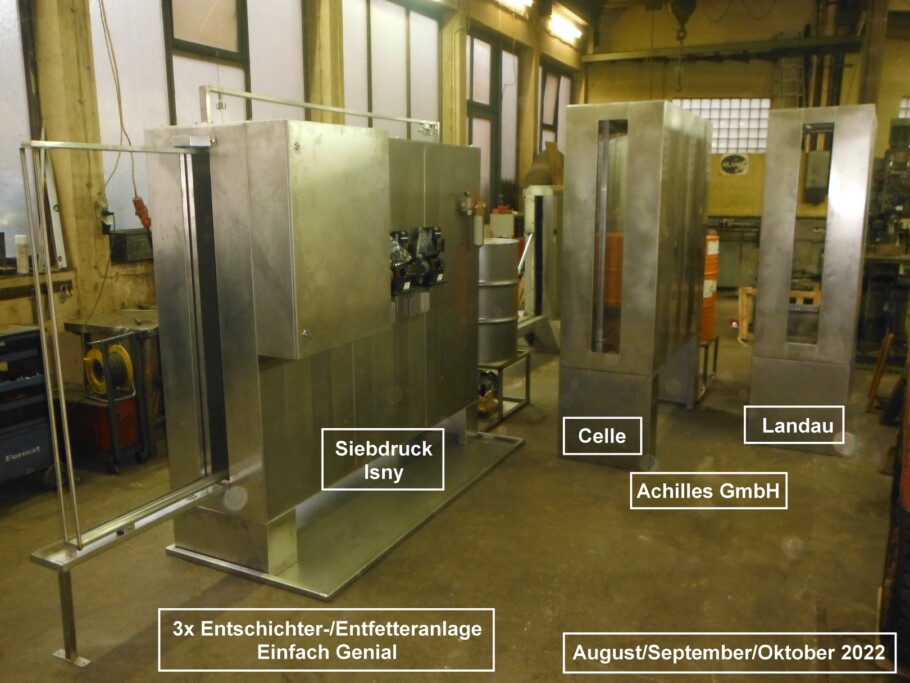
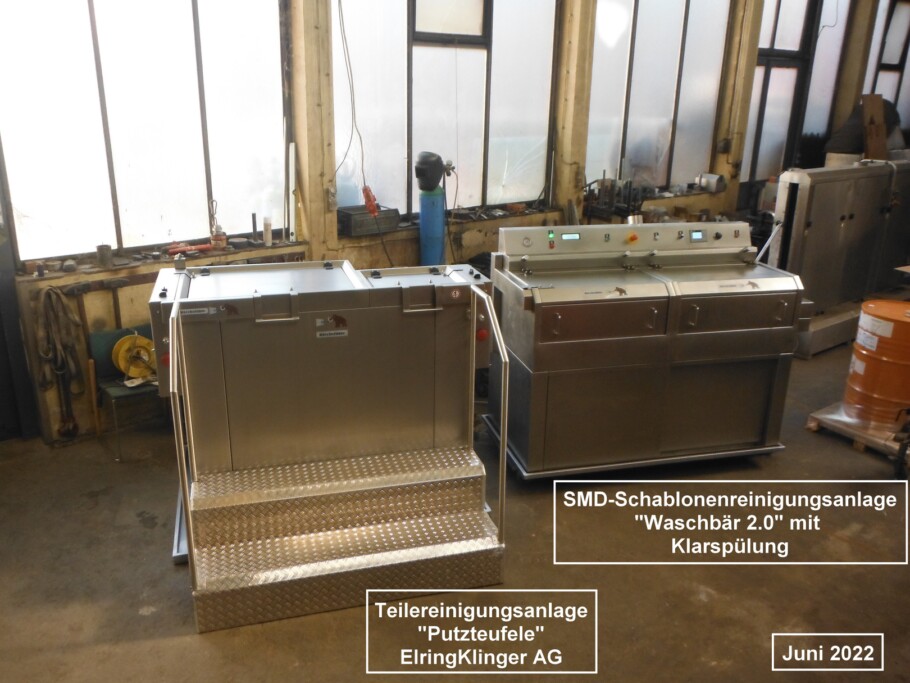
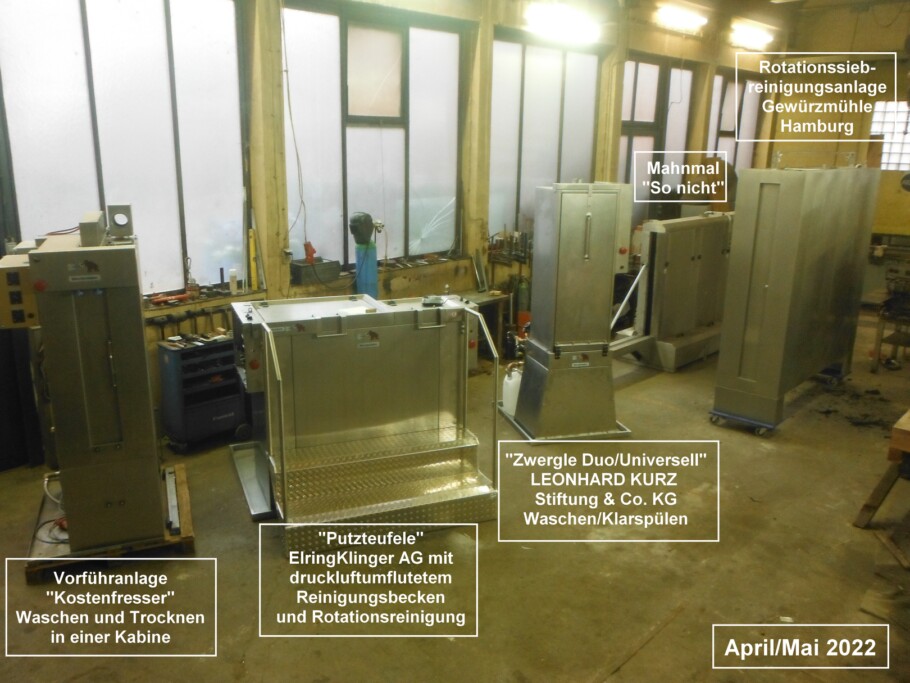
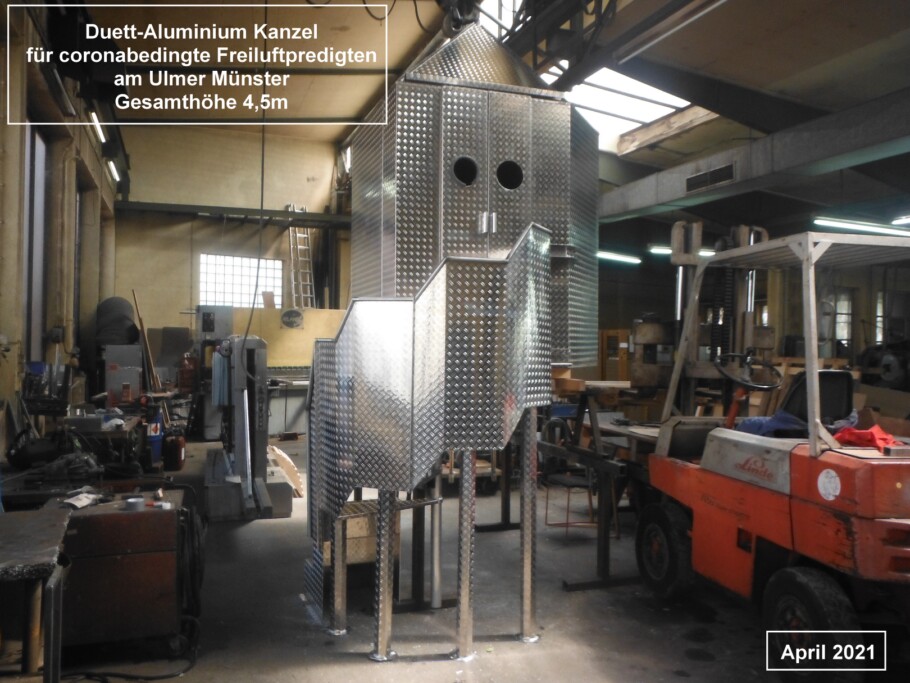
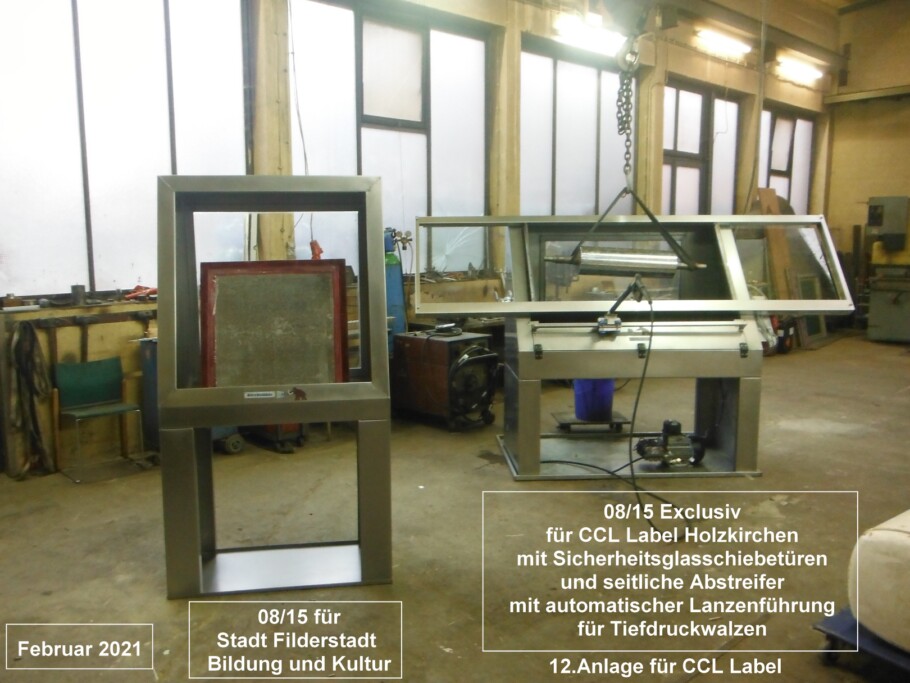
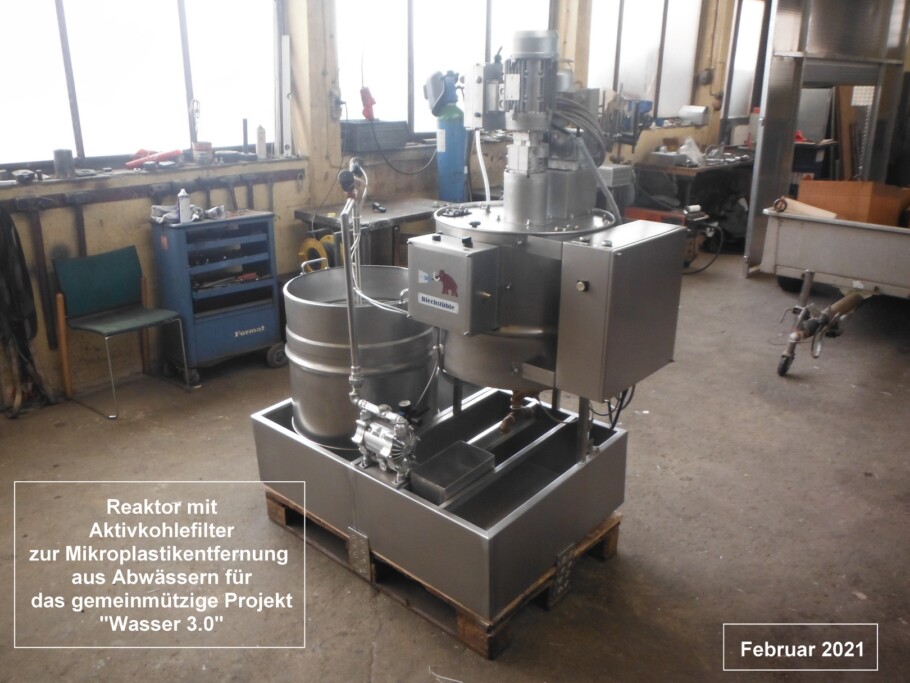
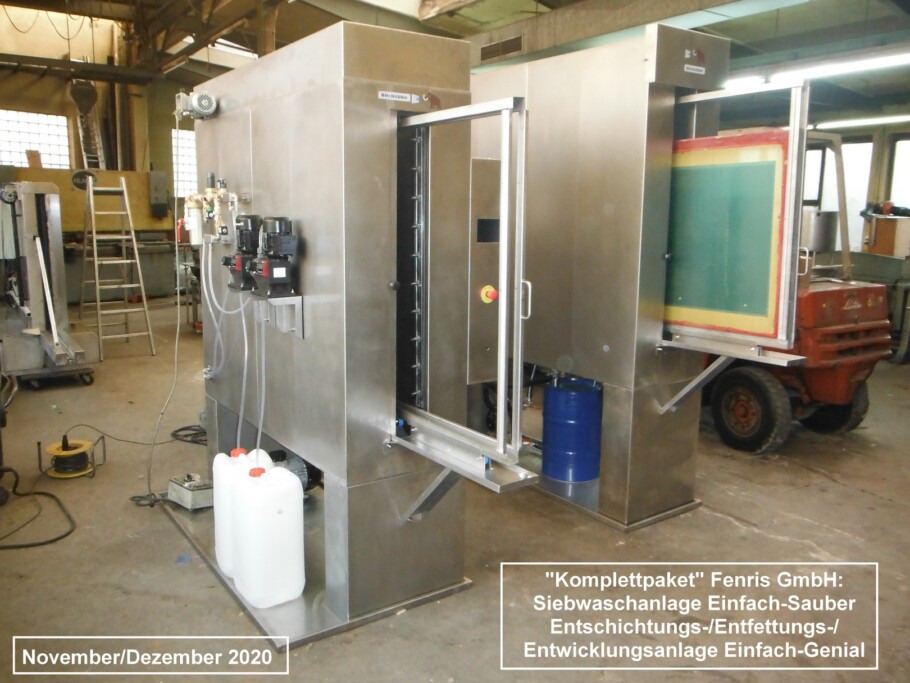
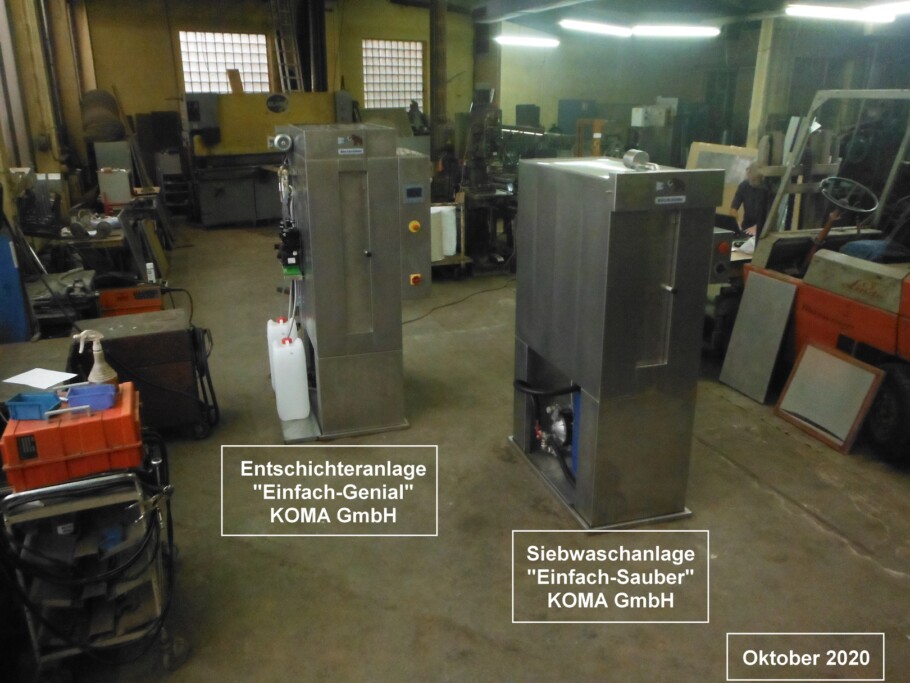
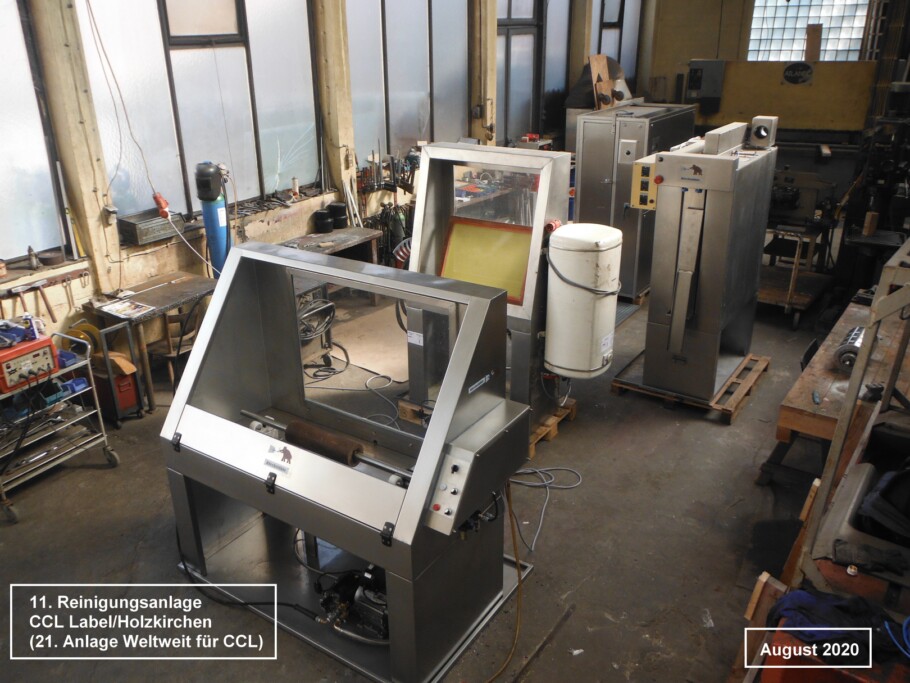
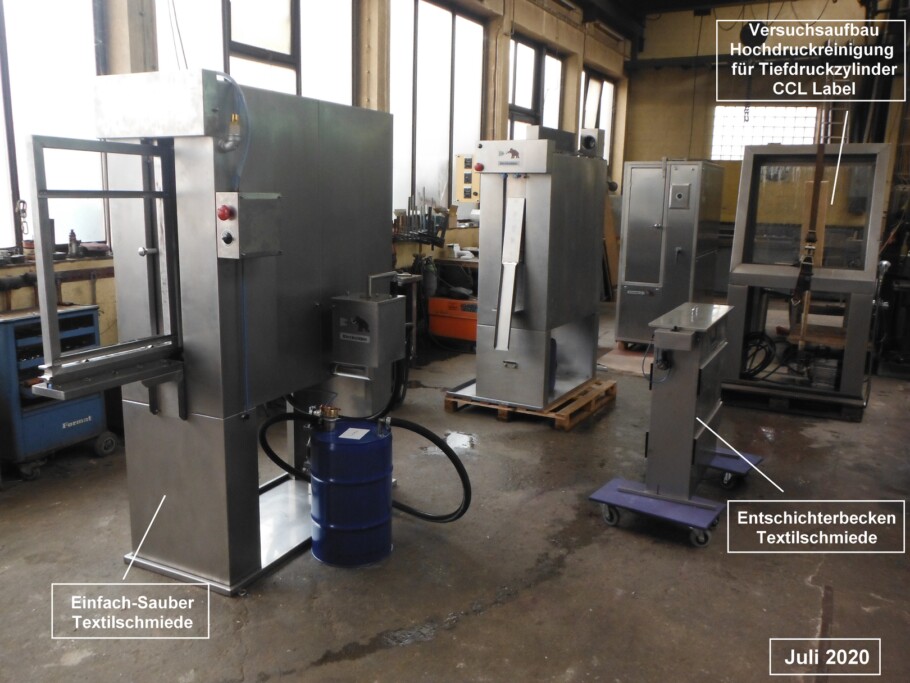
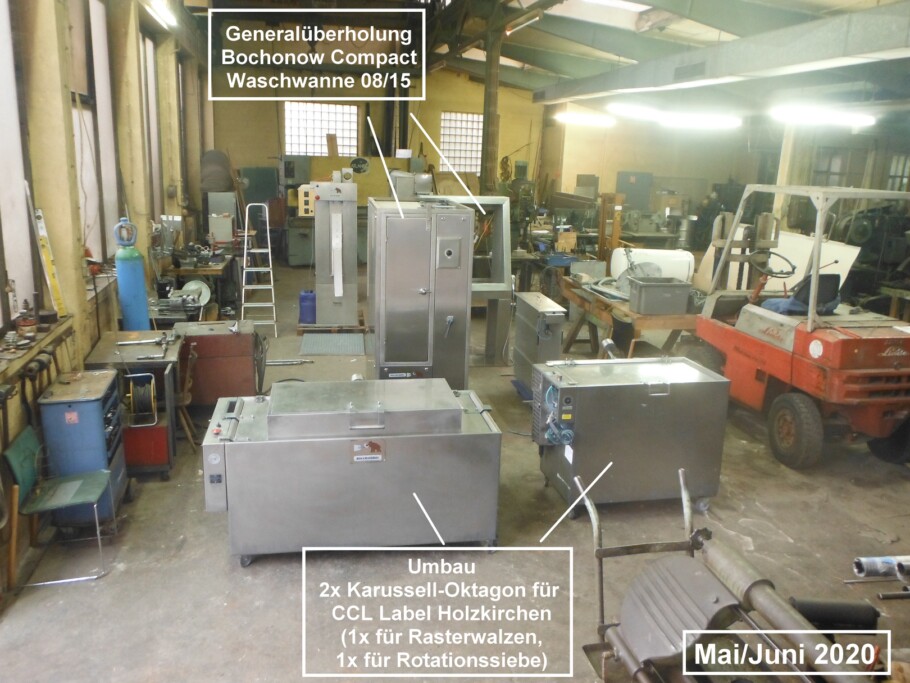
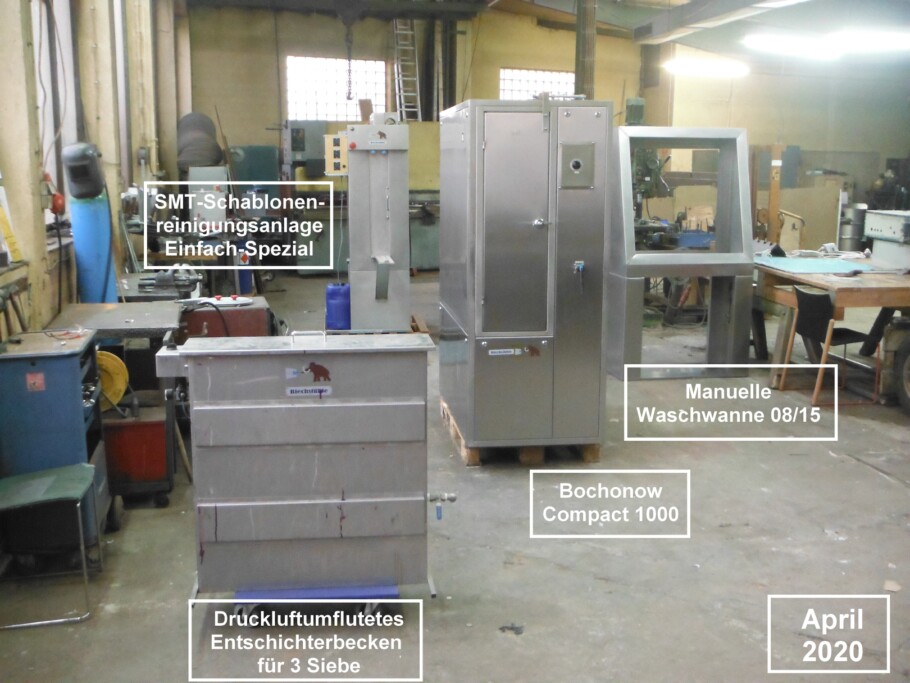
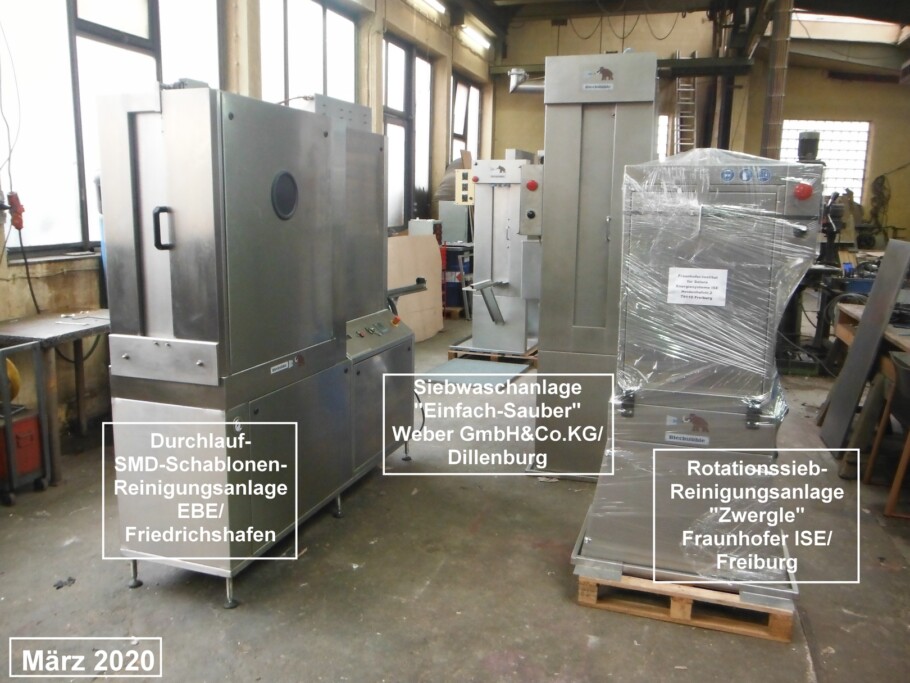
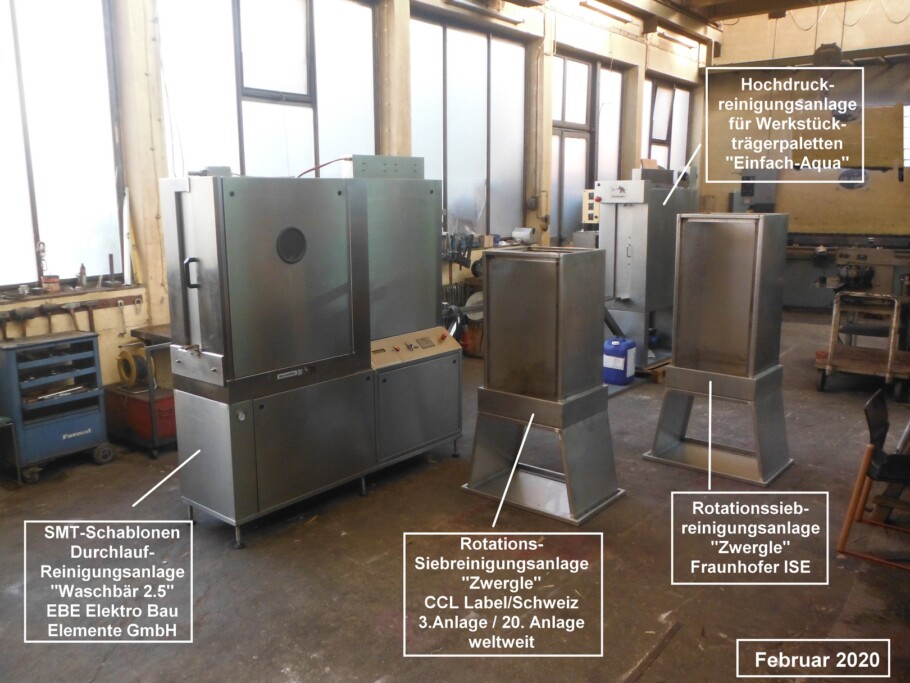
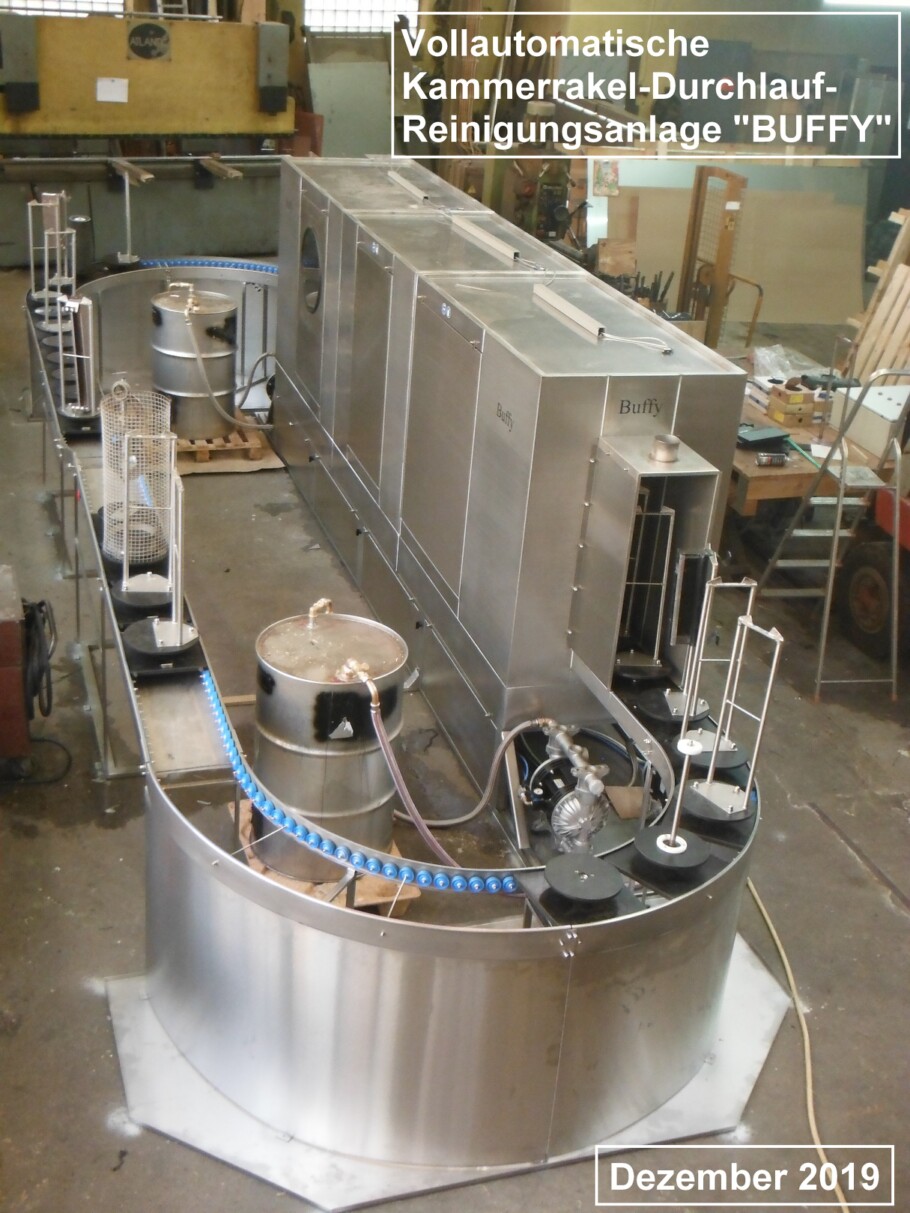
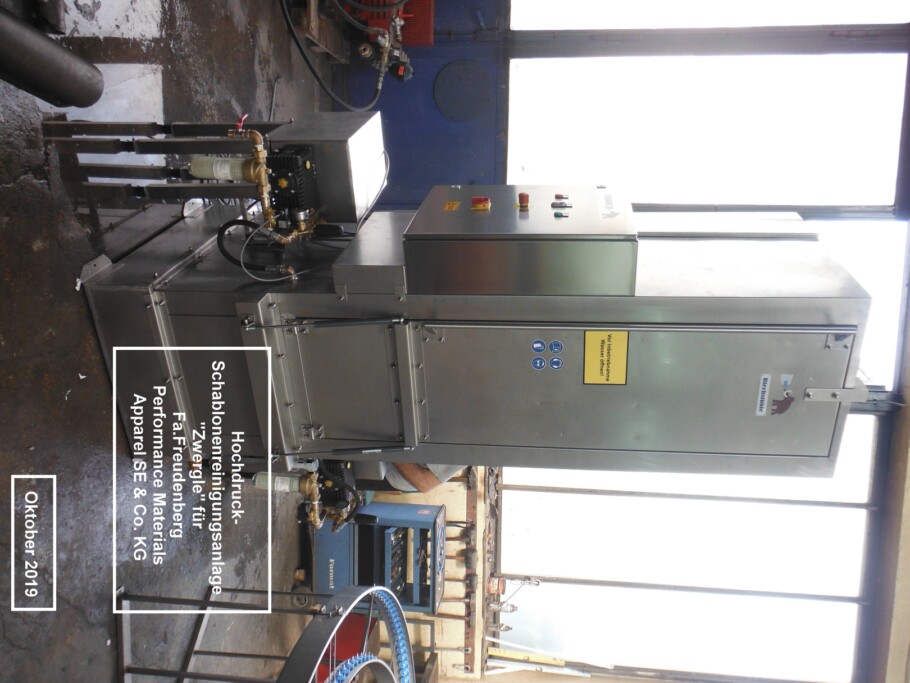
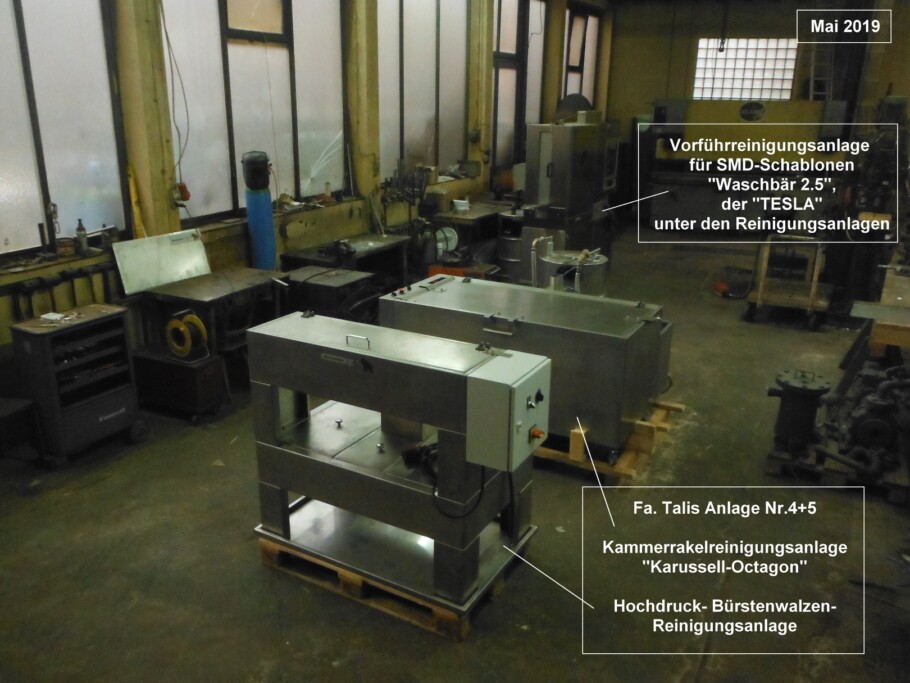
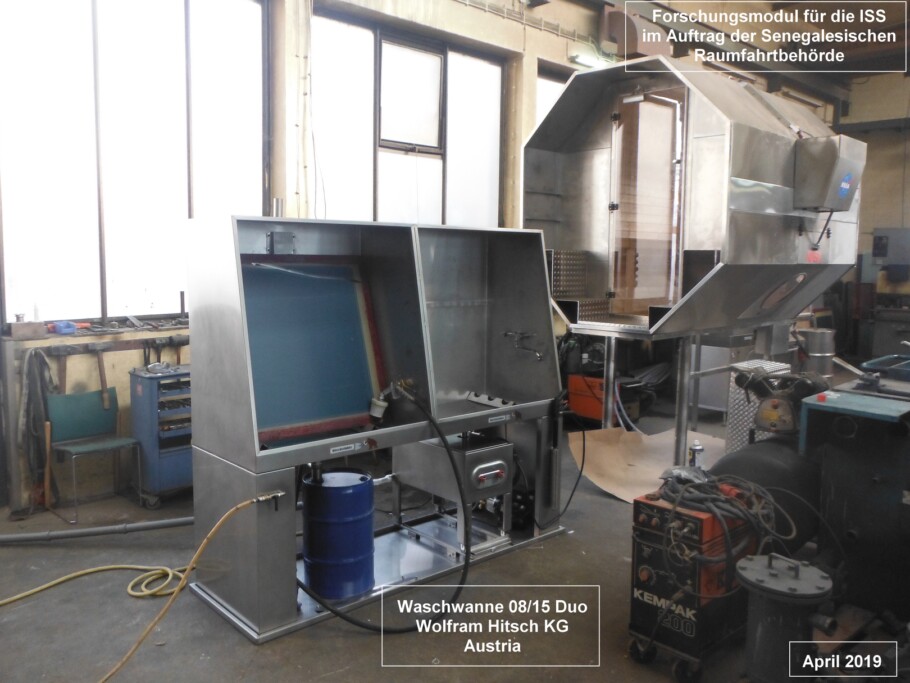
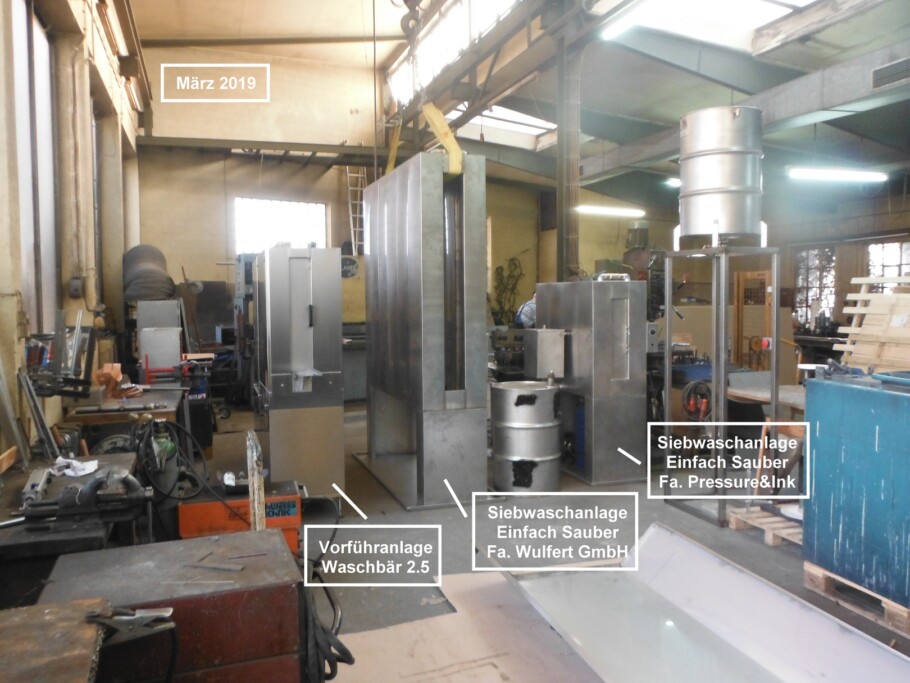
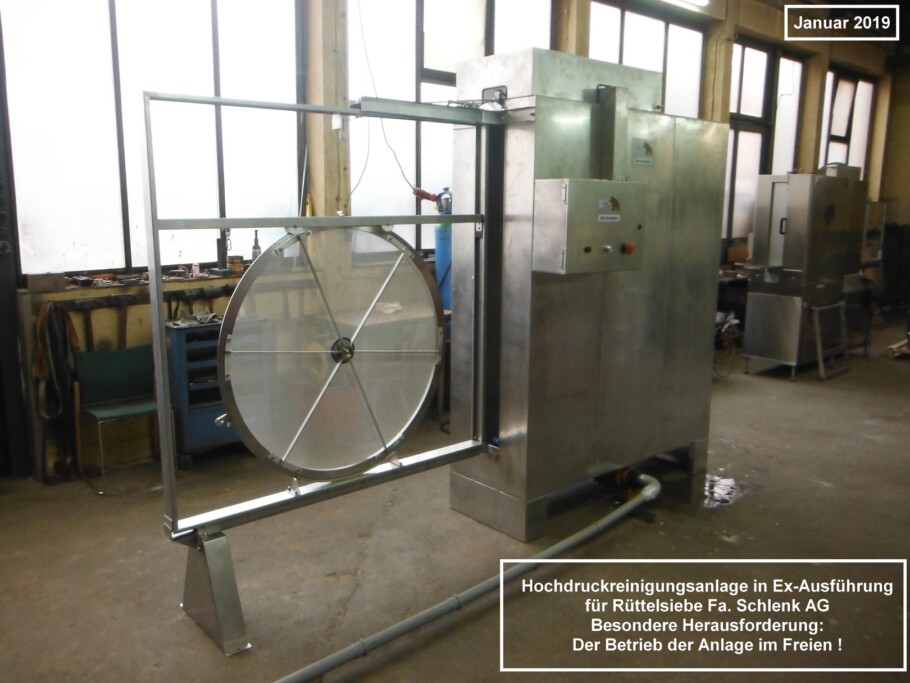

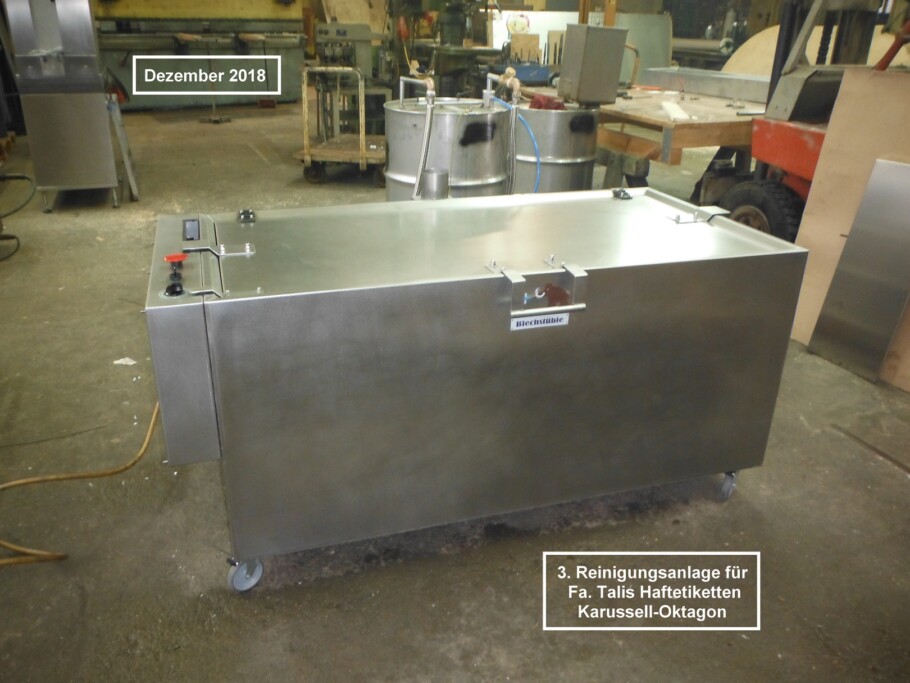
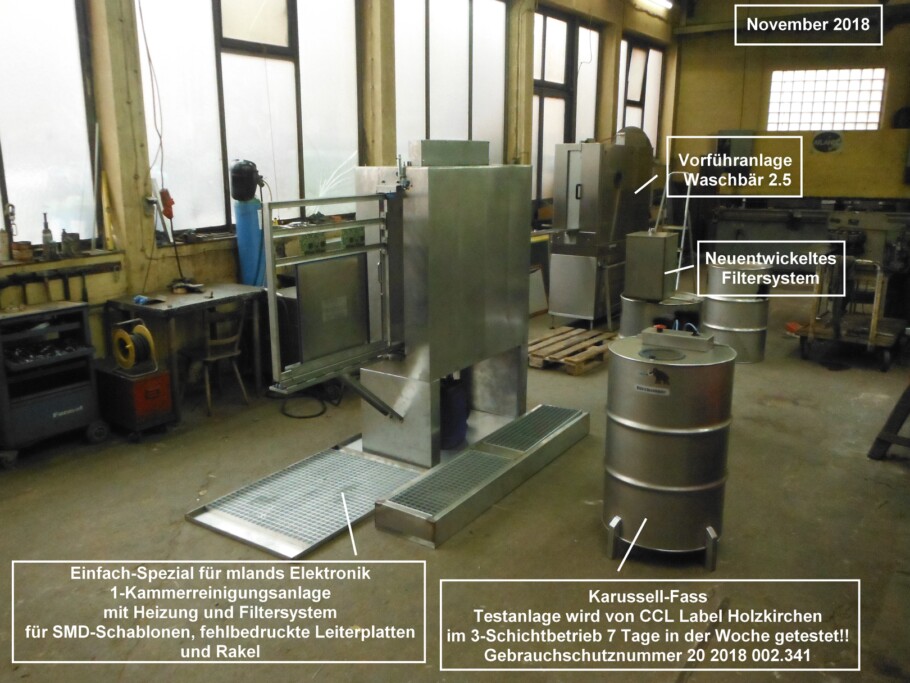
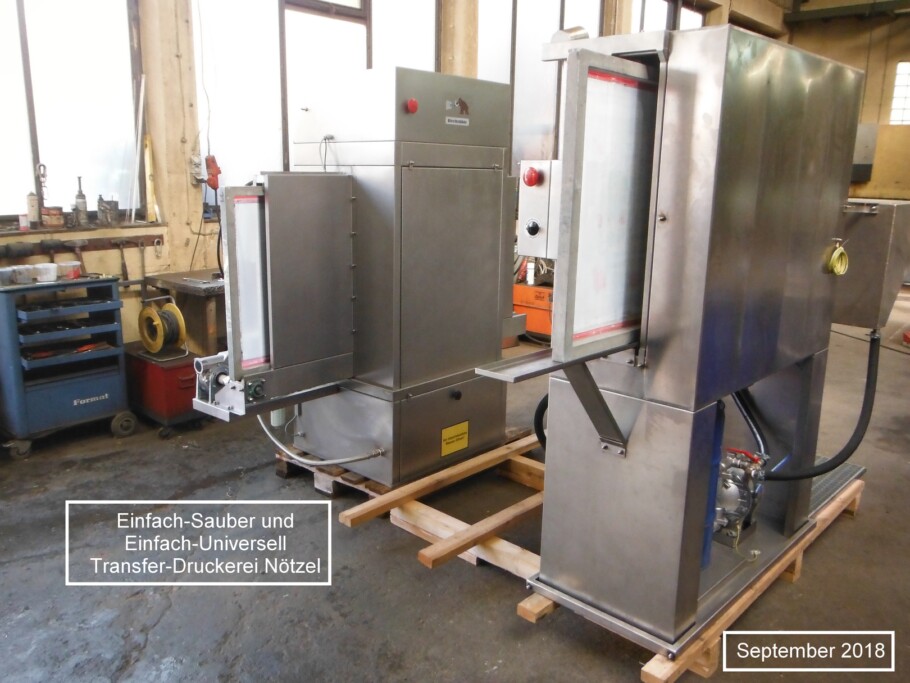
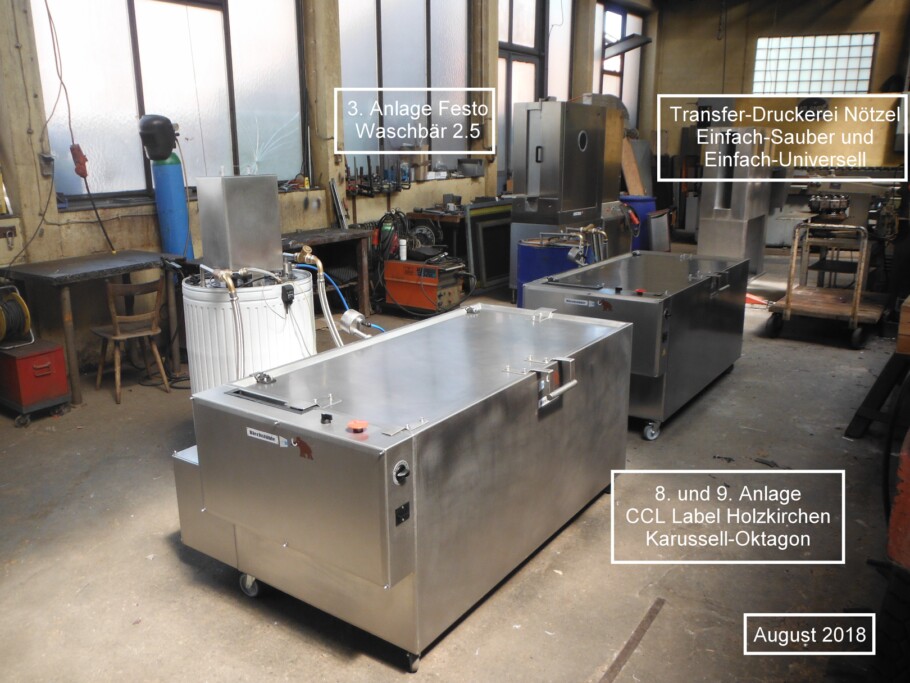
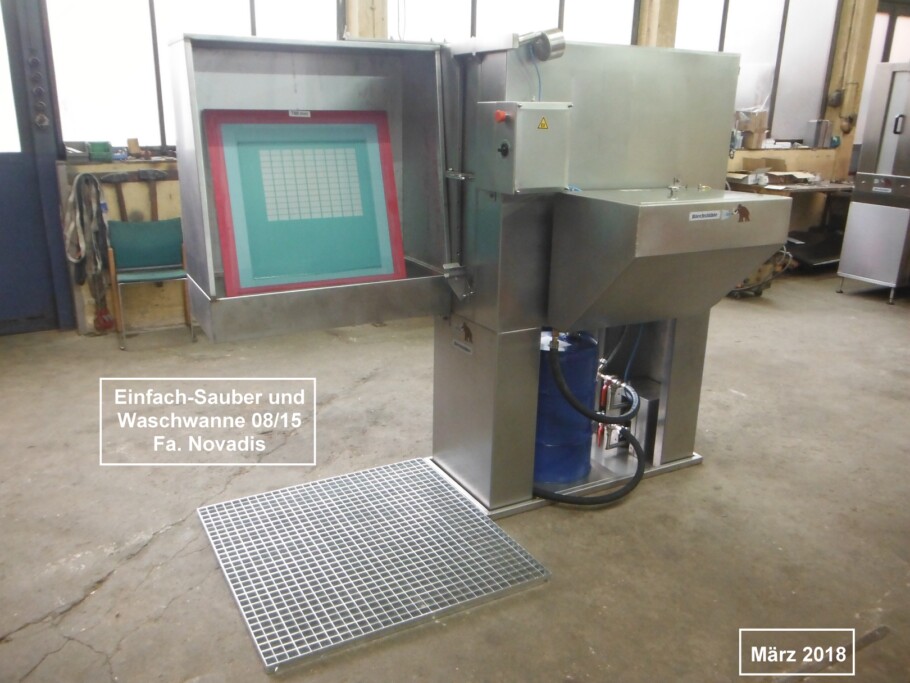
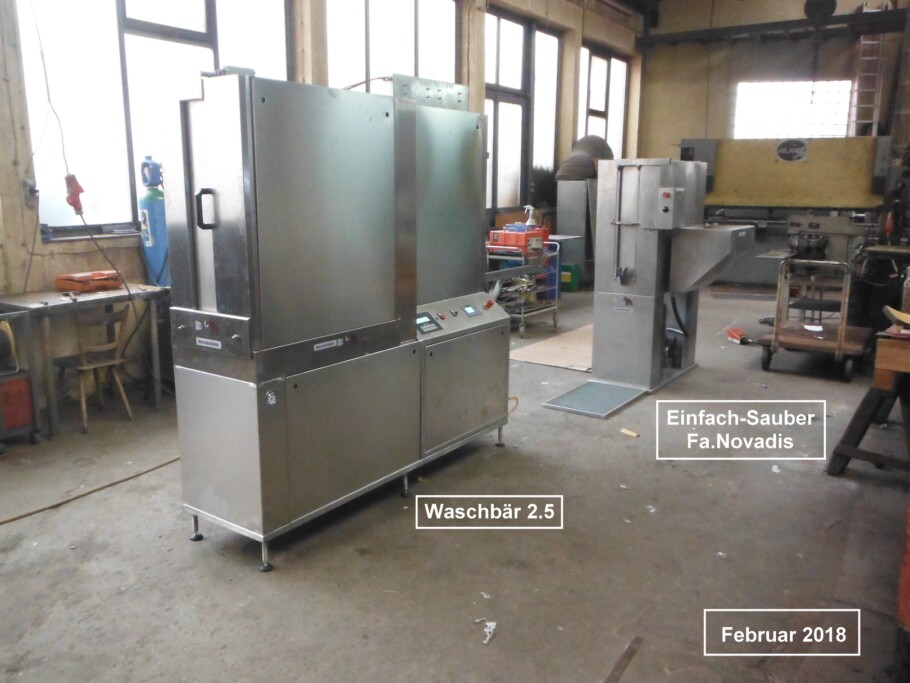
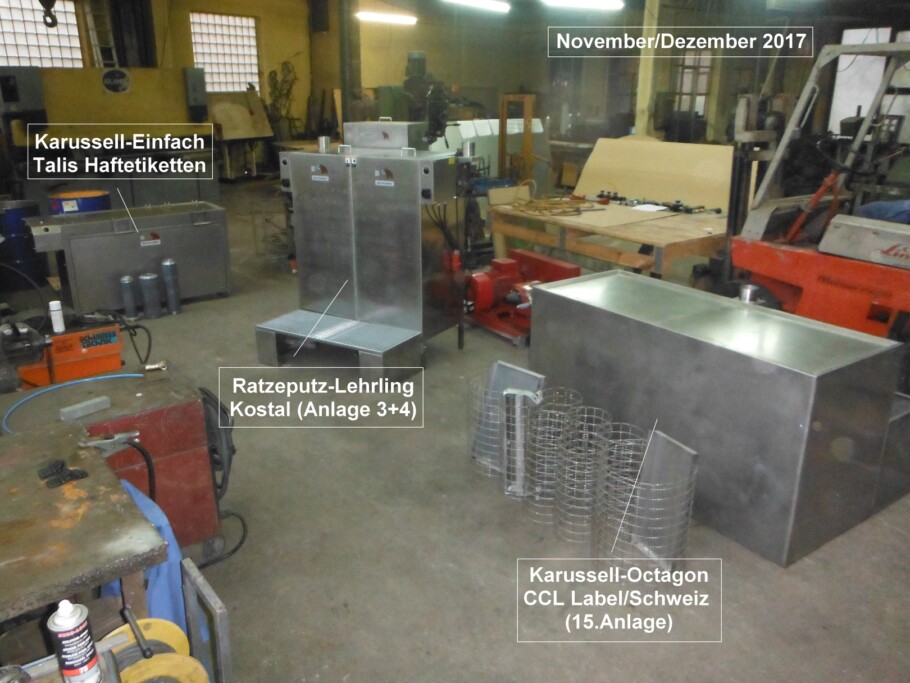
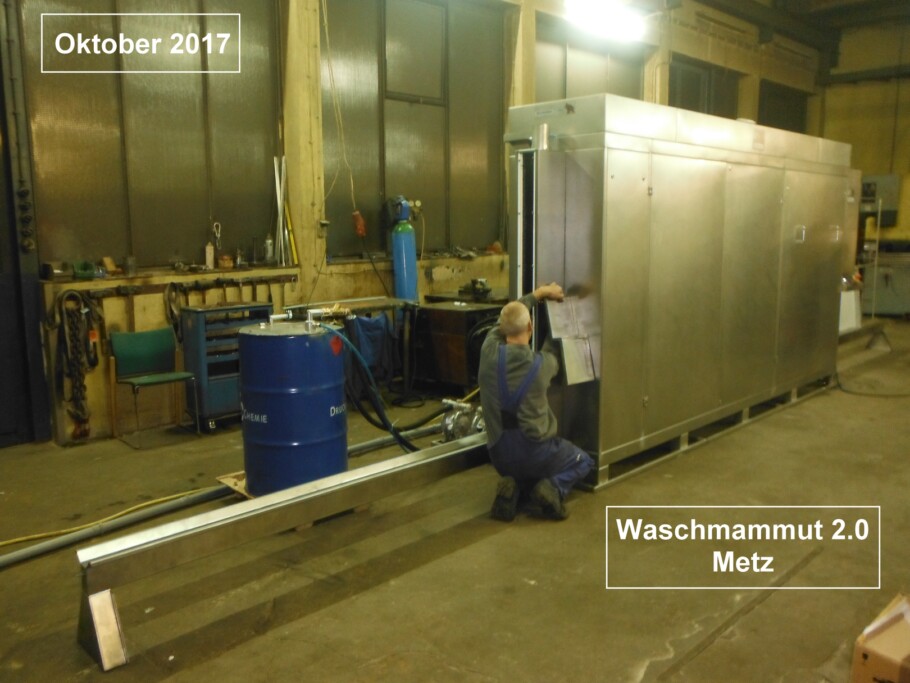
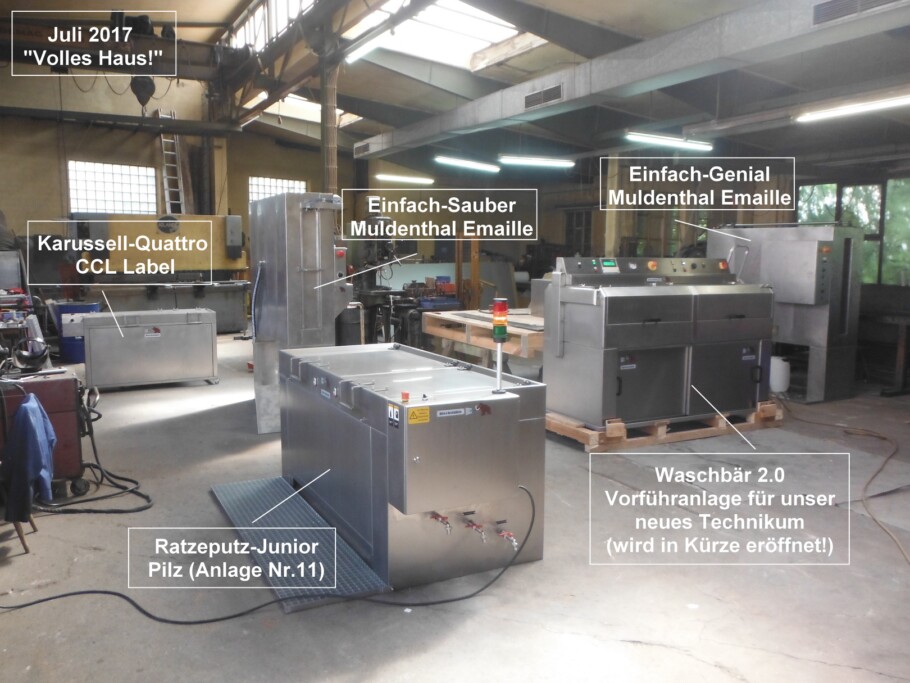
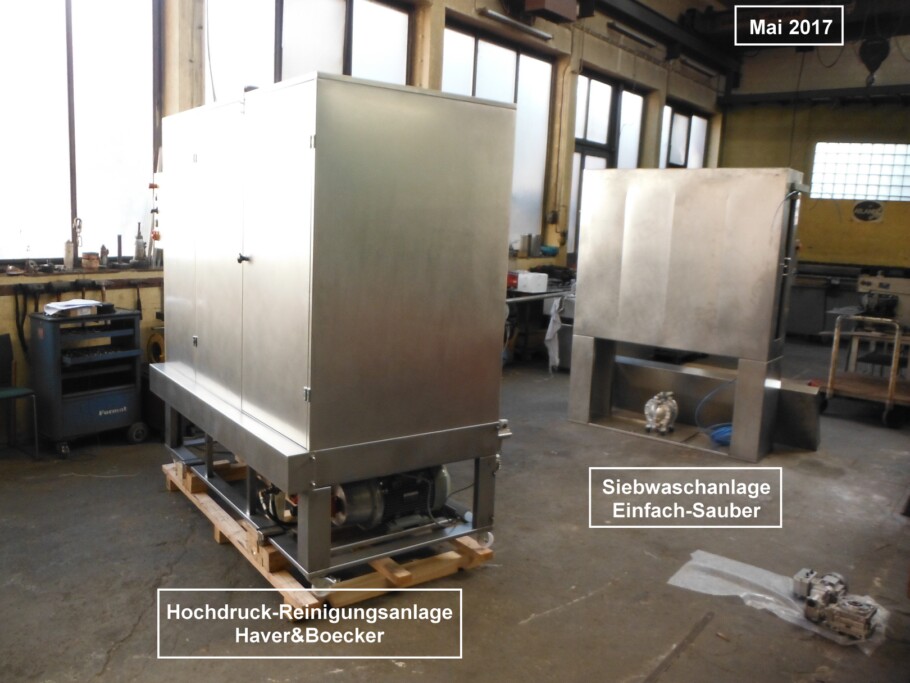
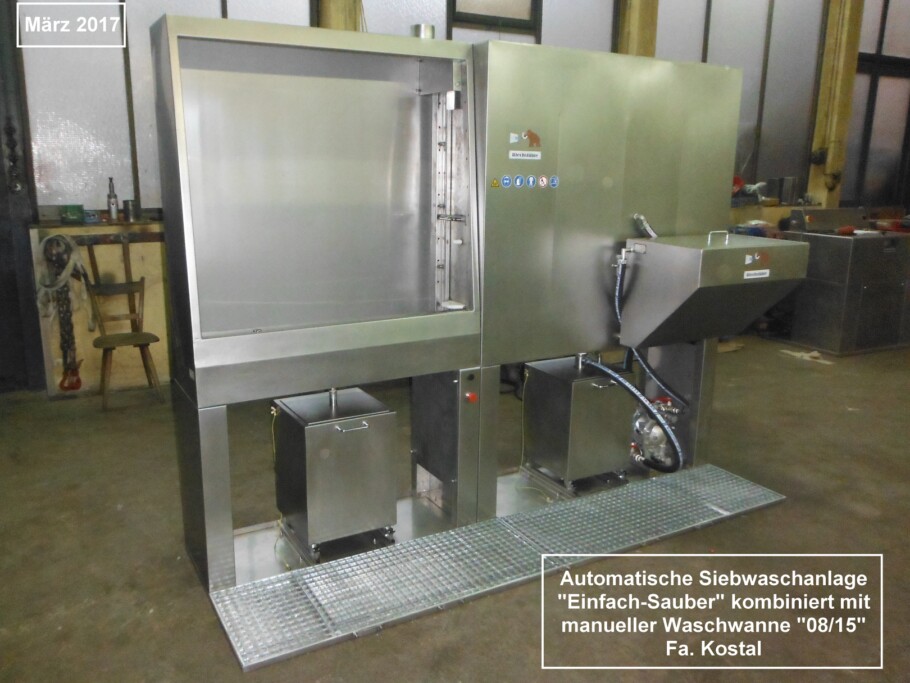
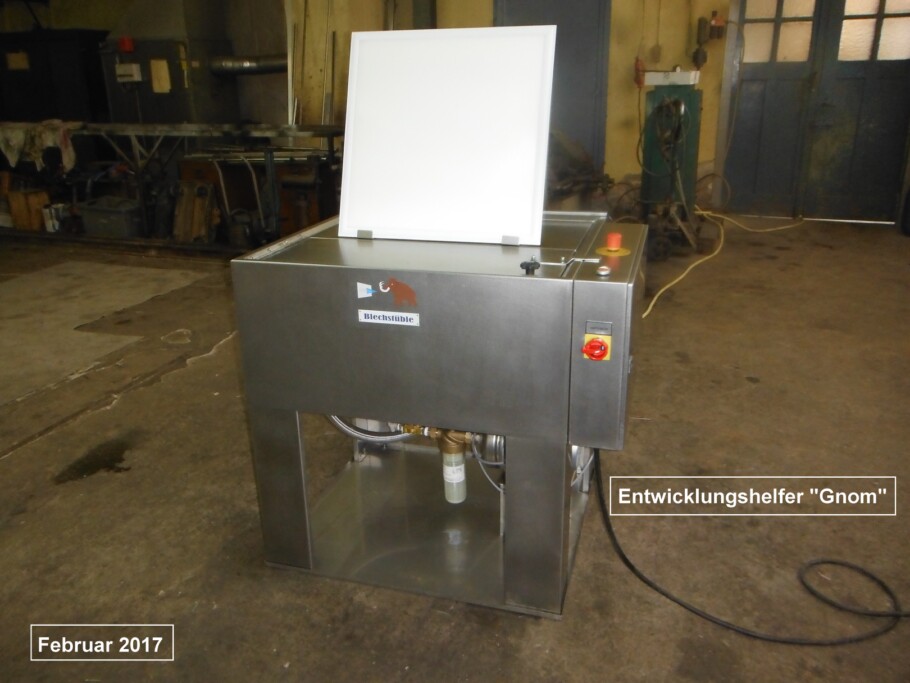
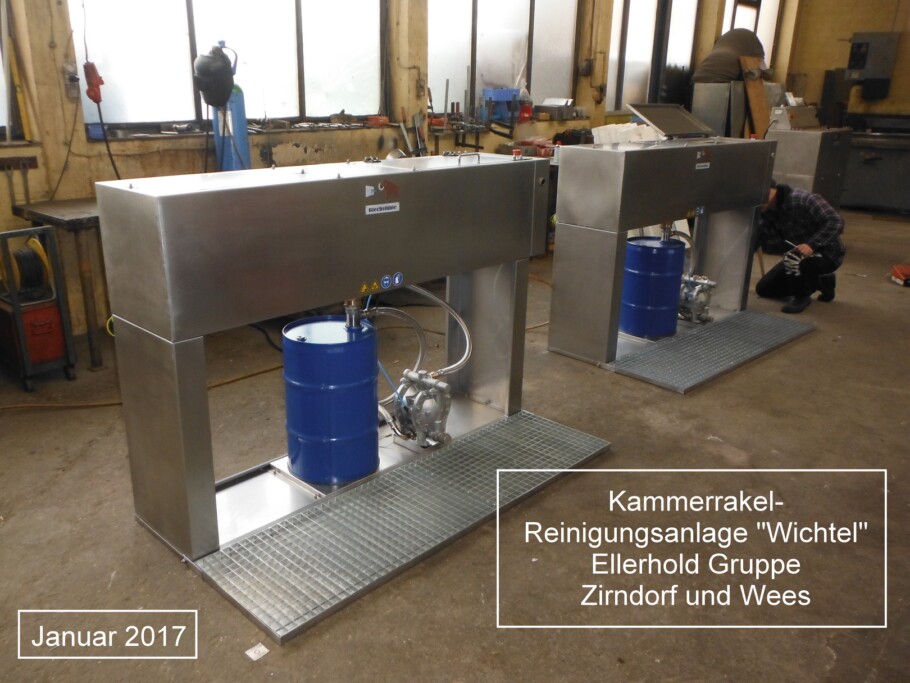
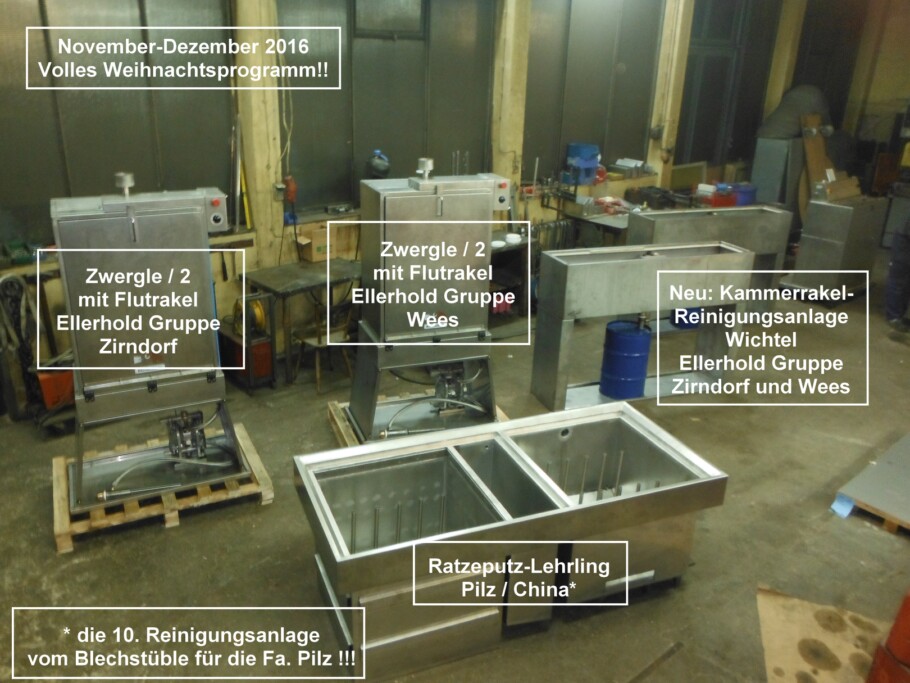
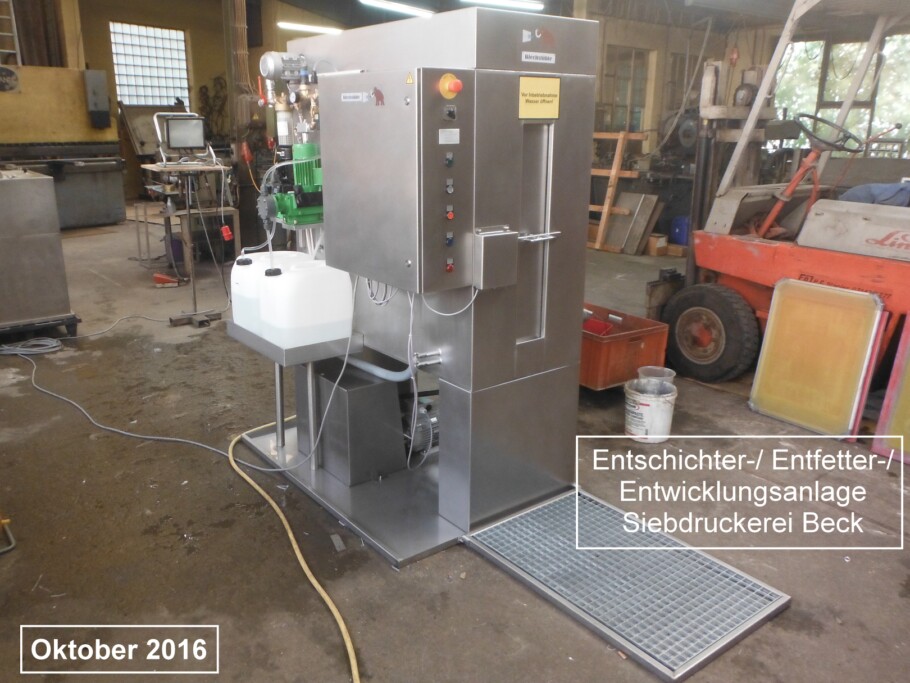
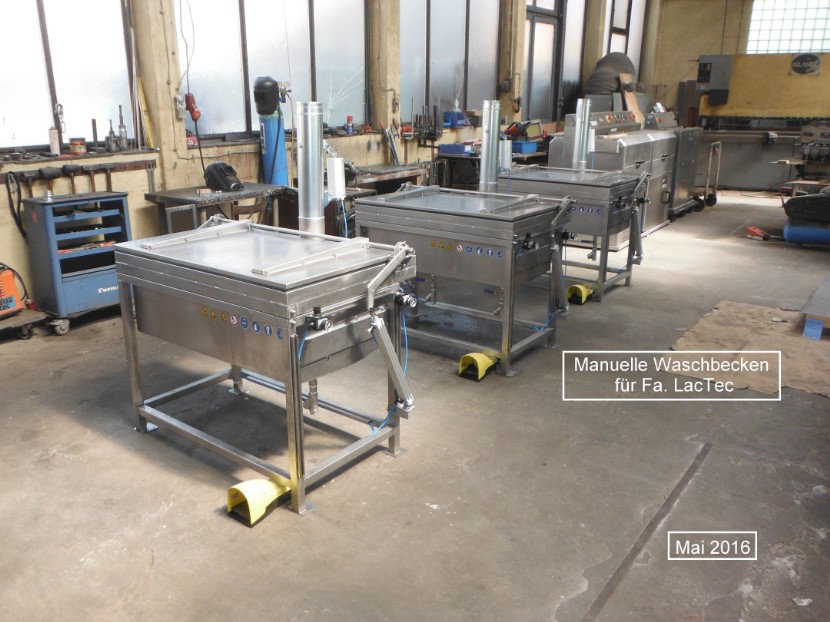
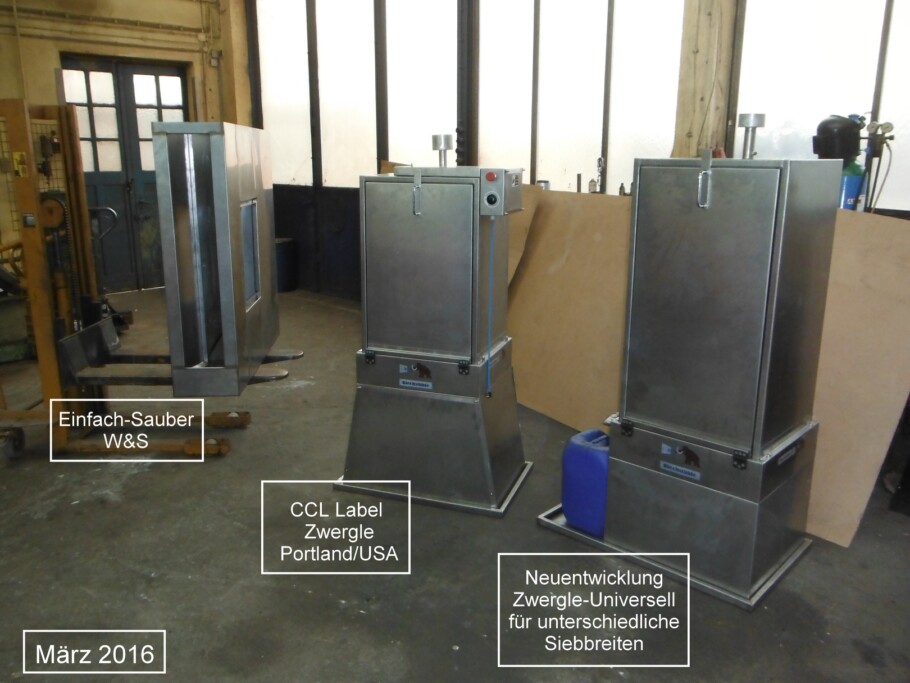
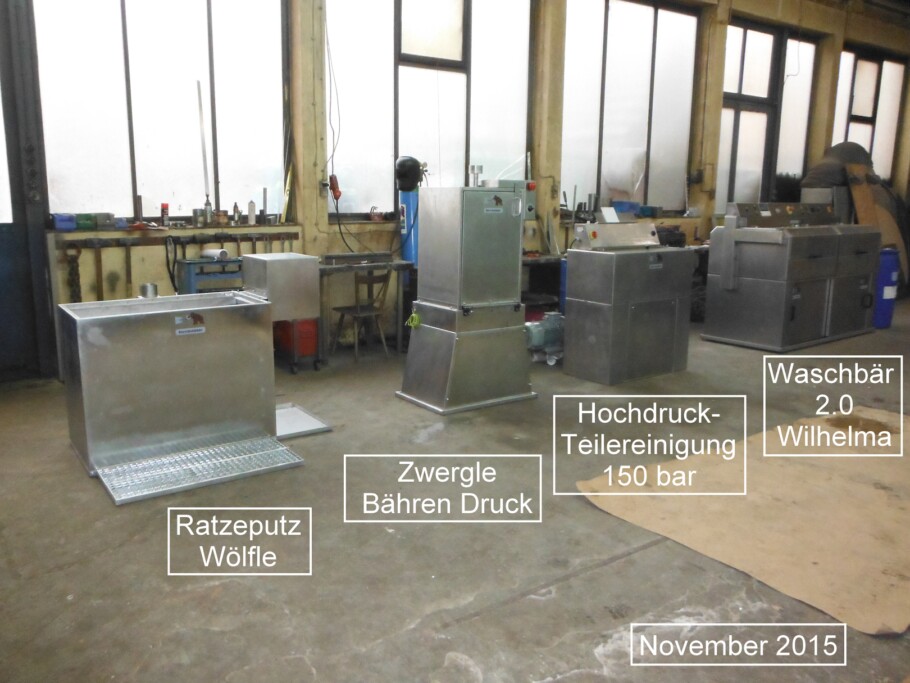
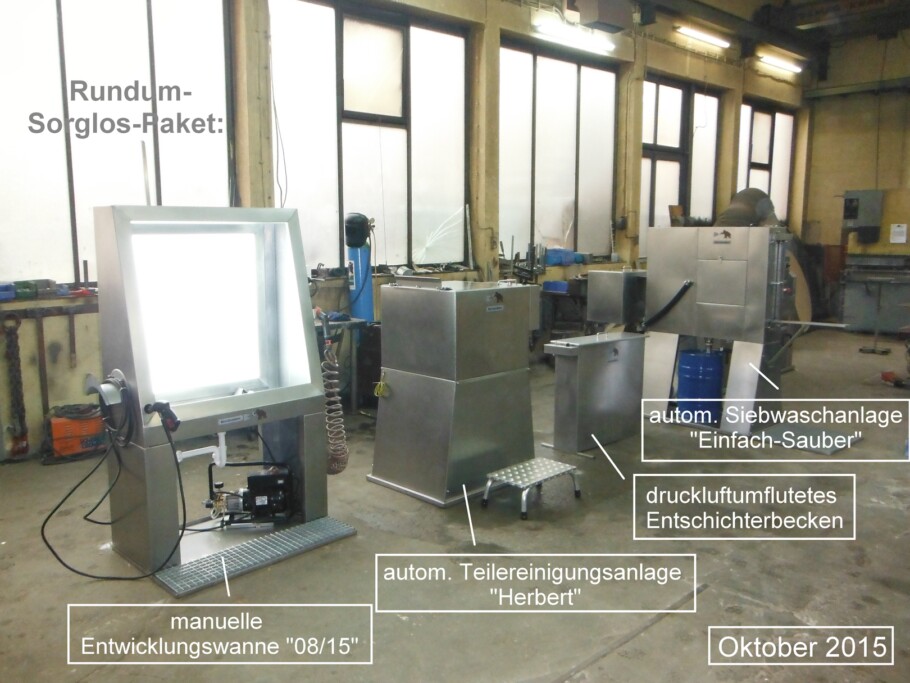
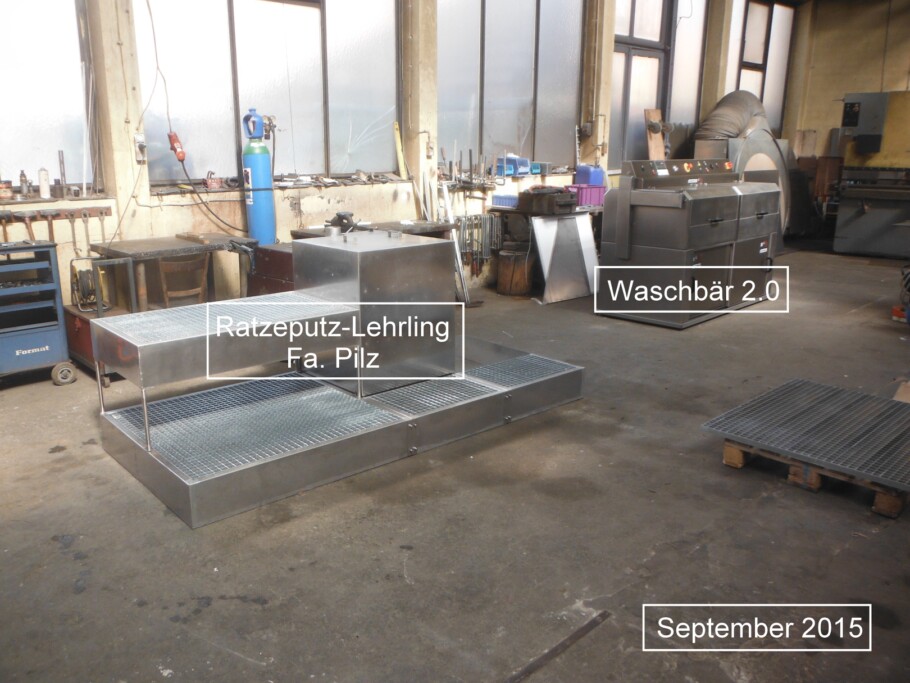
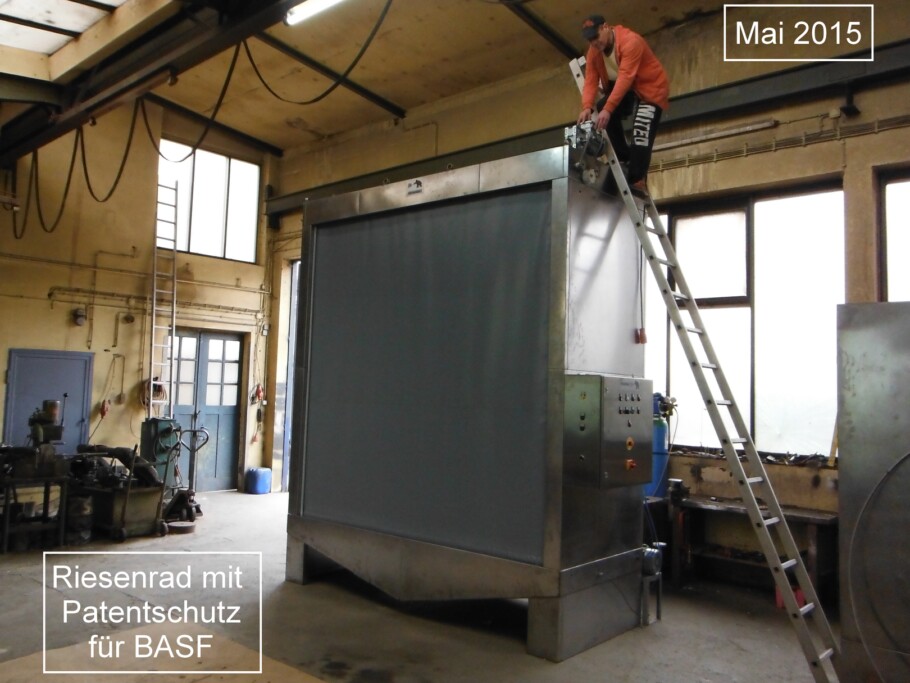
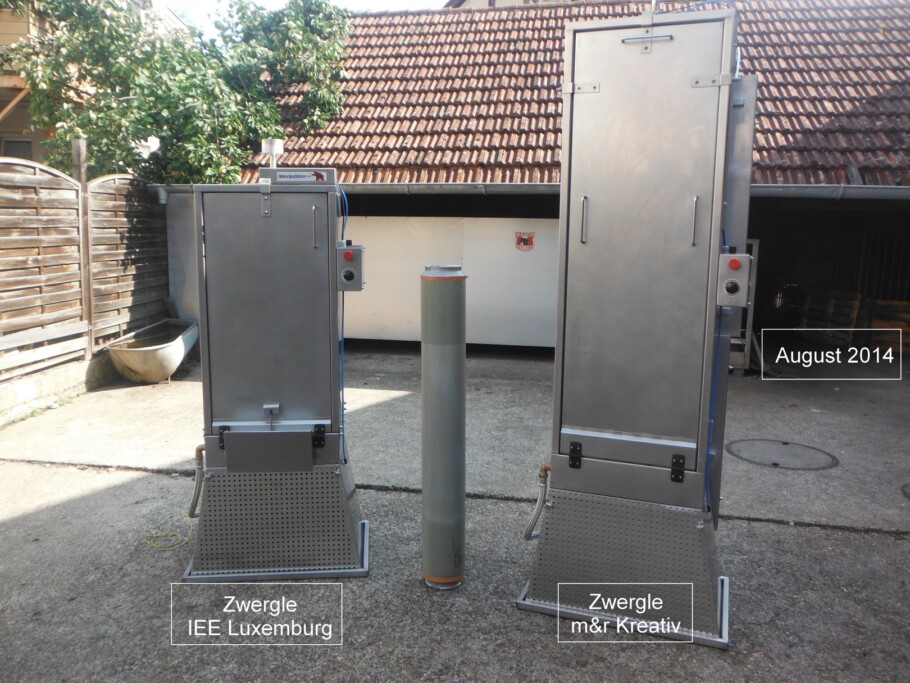
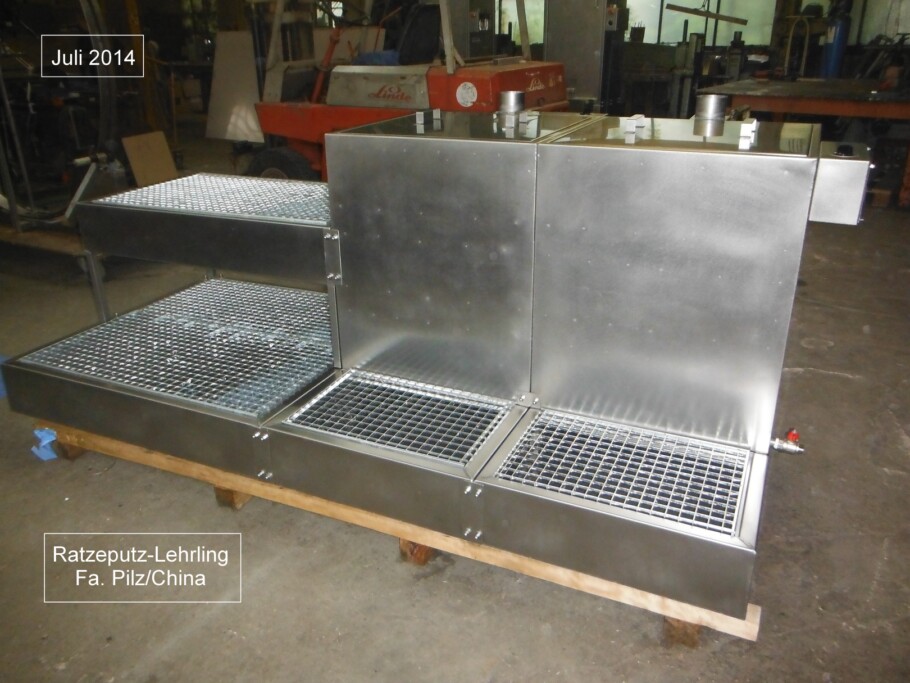
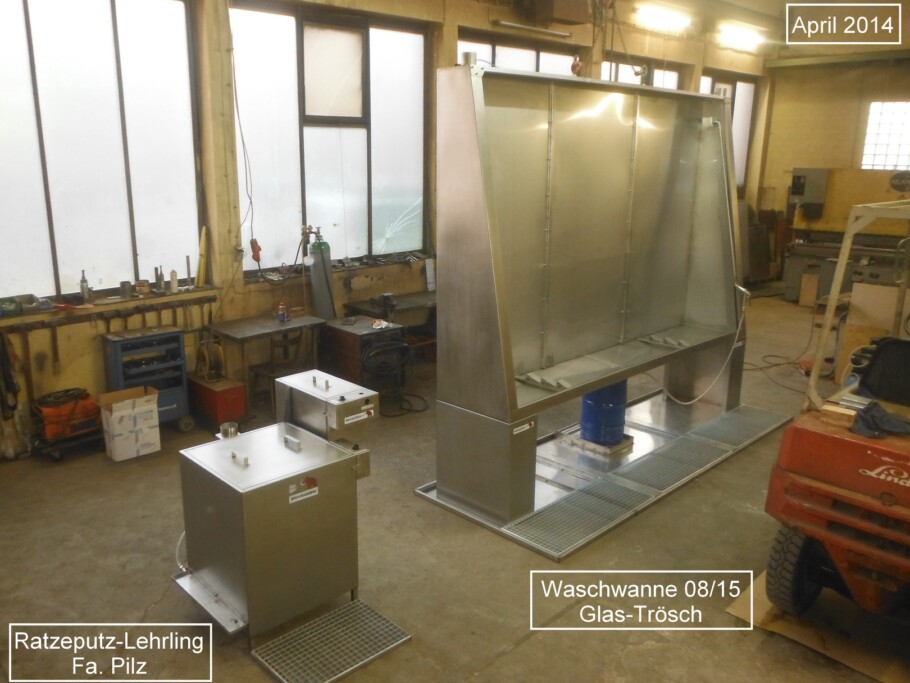
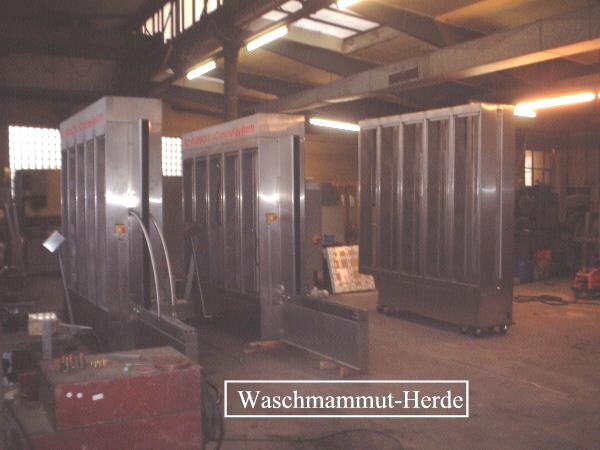
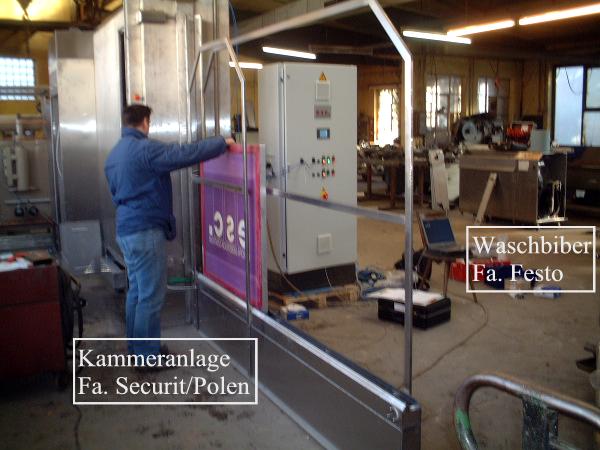
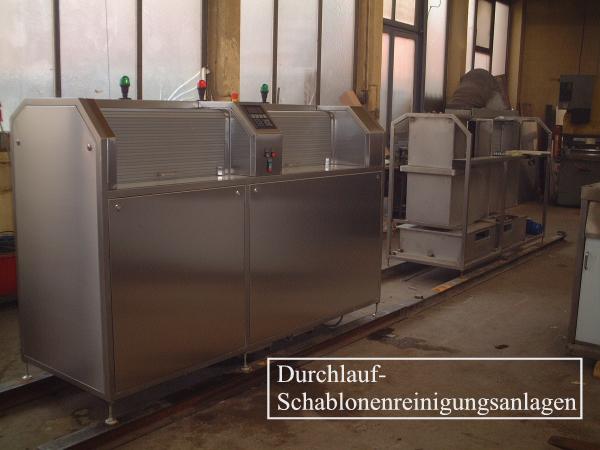
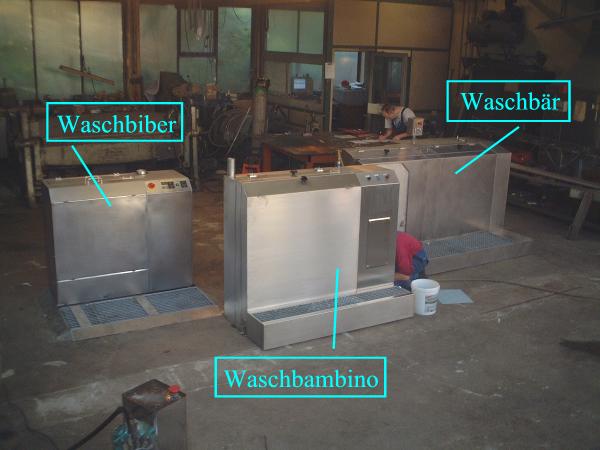
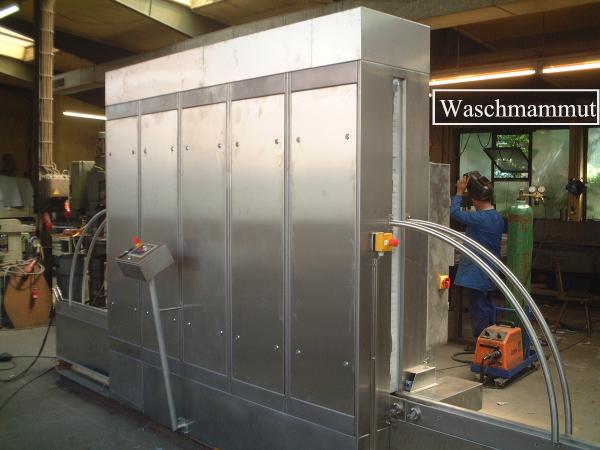